Lower furnace structure of pseudo-single crystal ingot furnace
An ingot furnace and quasi-single crystal technology, which is applied in the field of the lower furnace body mechanism of a quasi-single crystal ingot furnace, can solve problems such as high power consumption, unfavorable single crystal, and inability to meet the requirements of quasi-single crystal temperature gradient, and achieve shortening Effects of response time, simple structure, fast and efficient exception handling
- Summary
- Abstract
- Description
- Claims
- Application Information
AI Technical Summary
Problems solved by technology
Method used
Image
Examples
Embodiment Construction
[0028] attached Figure 1-9 It is a specific embodiment of the present invention. The invention is a lower furnace body mechanism of a quasi-single crystal ingot casting furnace, which includes a lower furnace bottom shell 1, an assembly support seat 2, a support seat 24 and a support column 25. The lower furnace bottom shell 1 is provided with a guide rail 11 transmission mechanism, A damper mechanism and a water-cooling mechanism, the damper mechanism includes a hot spot 12, the hot spot 12 of the damper mechanism is transmitted through the guide rail 11 transmission mechanism, and the corresponding damper mechanism is provided with a heating mechanism in the lower bottom shell 1, and the heating mechanism includes a heating rod 13 and The heating chamber 4 is provided with a plurality of heating rods 13, and the heating chamber 4 is provided with a DS block 5, and the four corners of the DS block 5 are respectively supported by the support columns 25 in the lower furnace bo...
PUM
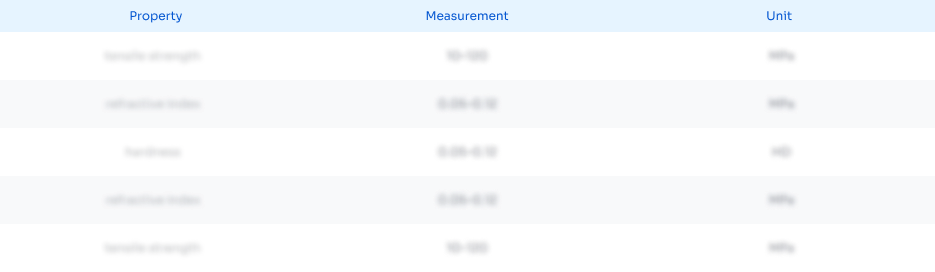
Abstract
Description
Claims
Application Information

- R&D
- Intellectual Property
- Life Sciences
- Materials
- Tech Scout
- Unparalleled Data Quality
- Higher Quality Content
- 60% Fewer Hallucinations
Browse by: Latest US Patents, China's latest patents, Technical Efficacy Thesaurus, Application Domain, Technology Topic, Popular Technical Reports.
© 2025 PatSnap. All rights reserved.Legal|Privacy policy|Modern Slavery Act Transparency Statement|Sitemap|About US| Contact US: help@patsnap.com