Hot reverse extrusion forming method for titanium alloy cup-shaped part
A technology of hot reverse extrusion and titanium alloy cup, applied in the direction of metal extrusion dies, etc., can solve the problems of uneven wall thickness distribution, uneven height of cup lugs, separation, etc., to improve dimensional accuracy and material utilization The effect of high efficiency, ensuring the uniformity of wall thickness and reducing manufacturing cost
- Summary
- Abstract
- Description
- Claims
- Application Information
AI Technical Summary
Problems solved by technology
Method used
Image
Examples
Embodiment Construction
[0028] The technical scheme of the present invention will be described in further detail below in conjunction with accompanying drawing and embodiment:
[0029] See attached figure 1 As shown, the extrusion mold used for the hot reverse extrusion forming method of titanium alloy cup-shaped parts includes an upper mold base 1, a punch 4, an extrusion sleeve 11, an extrusion cylinder 12, a lower mold base 13, and a push rod 14. It is characterized in that the floating punch 5 is connected to the bottom of the upper die base 1 by installing the back pressure spring I2 and the screw I3, and the pressing insert 8 is connected to the bottom of the floating punch 5 by installing the back pressure spring II6 and the screw II7. The floating punch 5 and the pressing insert 8 are linked with the upper die base 1, the outer edge flange of the pressing insert 8 is limited to the upper end surface of the extrusion cylinder 12, and the central step of the pressing insert 8 enters the extrusi...
PUM
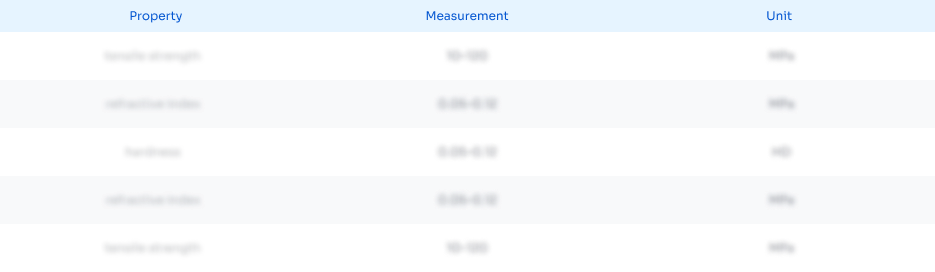
Abstract
Description
Claims
Application Information

- R&D
- Intellectual Property
- Life Sciences
- Materials
- Tech Scout
- Unparalleled Data Quality
- Higher Quality Content
- 60% Fewer Hallucinations
Browse by: Latest US Patents, China's latest patents, Technical Efficacy Thesaurus, Application Domain, Technology Topic, Popular Technical Reports.
© 2025 PatSnap. All rights reserved.Legal|Privacy policy|Modern Slavery Act Transparency Statement|Sitemap|About US| Contact US: help@patsnap.com