Method of using starch to reduce antimony oxide in low temperature molten salt
A technology of low-temperature molten salt and antimony oxide, applied in the field of antimony metallurgical process, can solve the problems of lower production efficiency, antimony volatilization loss, high melting temperature, etc., and achieve the effects of preventing combustion loss, improving utilization efficiency, and stabilizing technical indicators
- Summary
- Abstract
- Description
- Claims
- Application Information
AI Technical Summary
Problems solved by technology
Method used
Image
Examples
Embodiment 1
[0021] Sb in antimony oxide 2 o 3 The percentage by weight is 98.50%, the starch used is wheat starch, and both sodium carbonate and boron oxide are industrial grade reagents. Mix antimony oxide and starch at a mass ratio of 20 / 1 and add them to the conical stirring mixing tank, control the stirring speed of the main shaft to 20r / min, and the stirring speed of the auxiliary shaft to 60r / min, keep the mixing time for 60min, and then add the mixture to the circular For granulation in a disc granulator, the particle size of the pellets is required to be controlled at 8-10mm, and the pellets are dried at a temperature of 115°C to prepare the finished pellets for later use; mixing antimony oxide with sodium carbonate and boron oxide requires control of Na 2 O / Sb 2 o 3 mass ratio and B 2 o 3 / Sb 2 o 3 The mass ratios are 5 / 1 and 6 / 1 respectively. Add the above-mentioned mixed materials into a stainless steel crucible, heat up to 720°C to melt, and ensure that the stirring spe...
PUM
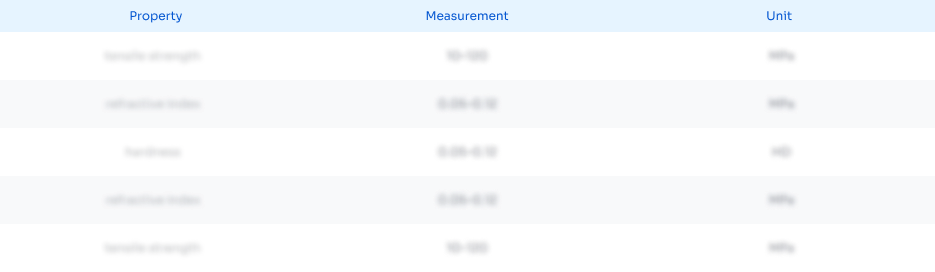
Abstract
Description
Claims
Application Information

- R&D Engineer
- R&D Manager
- IP Professional
- Industry Leading Data Capabilities
- Powerful AI technology
- Patent DNA Extraction
Browse by: Latest US Patents, China's latest patents, Technical Efficacy Thesaurus, Application Domain, Technology Topic, Popular Technical Reports.
© 2024 PatSnap. All rights reserved.Legal|Privacy policy|Modern Slavery Act Transparency Statement|Sitemap|About US| Contact US: help@patsnap.com