Method of temperature control and chromium preservation in rh decarburization process of ultra-low carbon high chromium steel
A decarburization process, high-chromium steel technology, applied in the field of steelmaking, can solve the problems of difficult temperature control of molten steel, difficult to achieve ultra-low carbon, high-chromium steel smelting, large loss of Cr alloy, etc., to reduce or LF heating power consumption and treatment time, improving RH treatment efficiency, and improving molten steel castability
- Summary
- Abstract
- Description
- Claims
- Application Information
AI Technical Summary
Problems solved by technology
Method used
Examples
Embodiment 1
[0029] 1) The temperature of molten steel in the RH station is 1615℃, Si content is 0.5%, Mn content is 1.5%, Cr content is 15%, and C content is 0.35%. After the ladle is in place, a three-stage pump is turned on to vacuum, and the vacuum chamber pressure drops below 100mbar. Start blowing oxygen, blowing 150-200Nm at a time 3 , The oxygen blowing is over, and then circulate for 2-5 minutes, then determine the oxygen, measure the temperature, take a sample to measure the carbon, determine the amount of oxygen blowing according to the carbon content, and repeat this operation until the C content drops below 0.1%.
[0030] 2) When the C content reaches below 0.1%, the four-stage vacuum pump is turned on, and when the pressure of the vacuum chamber is reduced to 5-20mbar, 100-150Nm of oxygen will be blown at one time 3 , The oxygen blowing is over, and then circulate for 2-5 minutes, then determine the oxygen, measure the temperature, take a sample to measure the carbon, determine th...
Embodiment 2
[0035] 1) The temperature of molten steel in the RH station is 1625℃, Si content is 0.05%, Mn content is 1.98%, Cr content is 5%, C content is 0.25%. After the ladle is in place, a three-stage pump is turned on to vacuum, and the vacuum chamber pressure drops below 100mbar. Start blowing oxygen, blowing 150-200Nm at a time 3 , The oxygen blowing is over, and then circulate for 2-5 minutes, then determine the oxygen, measure the temperature, take a sample to measure the carbon, determine the amount of oxygen blowing according to the carbon content, and repeat this operation until the C content drops below 0.1%.
[0036] 2) When the C content reaches below 0.1%, the four-stage vacuum pump is turned on, and when the pressure of the vacuum chamber is reduced to 5-20mbar, 100-150Nm of oxygen will be blown at one time 3 , The oxygen blowing is over, and then circulate for 2-5 minutes, then determine the oxygen, measure the temperature, take a sample to measure the carbon, determine the a...
Embodiment 3
[0041] 1) The temperature of molten steel in the RH station is 1605℃, Si content is 0.45%, Mn content is 0.51%, Cr content is 10%, C content is 0.11%. After the ladle is in place, a three-stage pump is turned on to vacuum, and the vacuum chamber pressure drops below 100mbar. Start blowing oxygen, blowing 150-200Nm at a time 3 , The oxygen blowing is over, and then circulate for 2-5 minutes, then determine the oxygen, measure the temperature, take a sample to measure the carbon, determine the amount of oxygen blowing according to the carbon content, and repeat this operation until the C content drops below 0.1%.
[0042] 2) When the C content reaches below 0.1%, the four-stage vacuum pump is turned on, and when the pressure of the vacuum chamber is reduced to 5-20mbar, 100-150Nm of oxygen will be blown at one time 3 , The oxygen blowing is over, and then circulate for 2-5 minutes, then determine the oxygen, measure the temperature, take a sample to measure the carbon, determine the ...
PUM
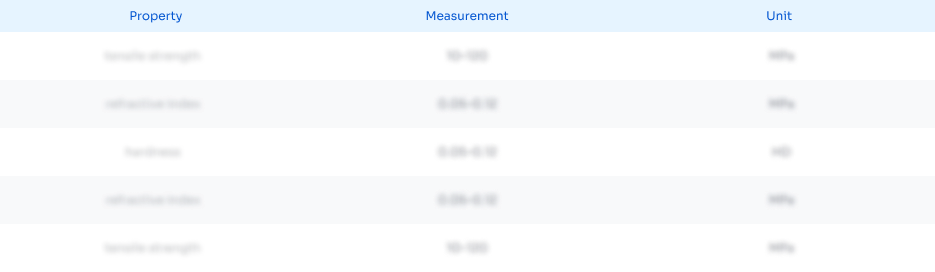
Abstract
Description
Claims
Application Information

- R&D Engineer
- R&D Manager
- IP Professional
- Industry Leading Data Capabilities
- Powerful AI technology
- Patent DNA Extraction
Browse by: Latest US Patents, China's latest patents, Technical Efficacy Thesaurus, Application Domain, Technology Topic, Popular Technical Reports.
© 2024 PatSnap. All rights reserved.Legal|Privacy policy|Modern Slavery Act Transparency Statement|Sitemap|About US| Contact US: help@patsnap.com