Direct injection engine air intake system carbon removal agent
A technology of air intake system and engine, which is applied in the direction of detergent compounding agent, detergent composition, detergent composition solvent, etc., and can solve the problems of not achieving carbon removal effect, destroying lubricating oil film, long disassembly and assembly time, etc. , achieve the effect of overcoming poor hydrolytic stability, high surface activity and rich foam
- Summary
- Abstract
- Description
- Claims
- Application Information
AI Technical Summary
Problems solved by technology
Method used
Image
Examples
Embodiment 1
[0046] The raw materials of carbon removal agent for direct injection engine air intake system are as follows: 60% volatile solvent, 20% polymer bipolar polyetheramine, 15% solvent-based surfactant, 1% silicone gemini surfactant, fuel friction modifier 1%, rust inhibitor 2%, deionized water 1%. Among them, the rust inhibitor is coconut acid diethanolamide, the volatile solvent is methanol, the fuel friction modifier is Akzo Nobel’s Adsee 600, the solvent-based surfactant is Steposol MET-10U from Stepan, and the polymer bipolar polyether The amine is Huntsman's ED2003, and the silicone gemini surfactant is Compound 11.
[0047] Preparation method: at room temperature, first add volatile solvent to the reactor, then add other raw materials, mix and stir evenly.
[0048] figure 2 Inspect the intake valve for the endoscope before cleaning, image 3 In order to use the carbon remover prepared in this example to clean the endoscope to detect the intake valve. The model is a 201...
Embodiment 2
[0050] The raw materials of carbon remover for direct injection engine air intake system are as follows: 40% volatile solvent, 30% polymer bipolar polyetheramine, 5% solvent-based surfactant, 10% silicone gemini surfactant, fuel friction modifier 3%, antirust agent 2%, deionized water 10%. Among them, the antirust agent is coconut oil monoethanolamide, the volatile solvent is toluene, the fuel friction modifier is Adsee 600 from Akzo Nobel, the solvent-based surfactant is Steposol MET-10U from Stepan, and the polymer bipolar polyether The amine is Huntsman's ED900, and the silicone gemini surfactant is Compound 11.
[0051] Preparation method: at room temperature, first add volatile solvent to the reactor, then add other raw materials, mix and stir evenly.
Embodiment 3
[0053] The raw materials of carbon removal agent for direct injection engine air intake system are as follows: 30% volatile solvent, 25% polymer bipolar polyetheramine, 20% solvent-based surfactant, 5% silicone gemini surfactant, fuel friction modifier 5%, rust inhibitor 10%, deionized water 5%. Among them, the rust inhibitor is 5% oleic acid monoethanolamide and lauric acid diethanolamide 5%, the volatile solvent is ethanol 15%, ethylene glycol butyl ether 15%, the fuel friction modifier is Lubrizol 9525A, solvent-based surface active The agent is Steposol MET-10U of Stepan, and the polymer bipolar polyether amine is Huntsman's ED2003 silicone gemini surfactant is compound 12.
[0054] Preparation method: at room temperature, first add volatile solvent to the reactor, then add other raw materials, mix and stir evenly.
PUM
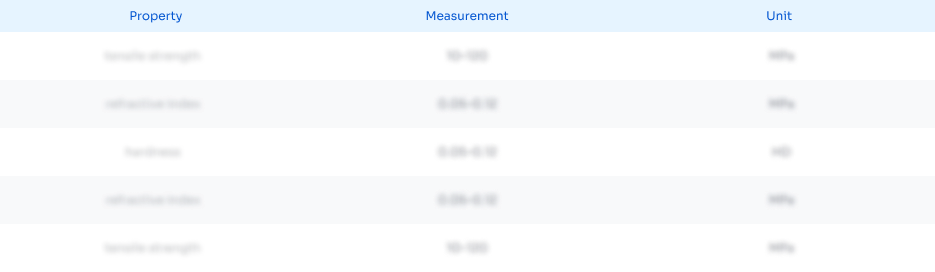
Abstract
Description
Claims
Application Information

- Generate Ideas
- Intellectual Property
- Life Sciences
- Materials
- Tech Scout
- Unparalleled Data Quality
- Higher Quality Content
- 60% Fewer Hallucinations
Browse by: Latest US Patents, China's latest patents, Technical Efficacy Thesaurus, Application Domain, Technology Topic, Popular Technical Reports.
© 2025 PatSnap. All rights reserved.Legal|Privacy policy|Modern Slavery Act Transparency Statement|Sitemap|About US| Contact US: help@patsnap.com