Water-saving and environment-friendly chlorinated polyethylene production method
A technology of chlorinated polyethylene and its production method, which is applied in the field of chlorinated polyethylene rubber preparation, can solve problems such as corrosion and unclean acid washing, and achieve the effects of saving water resources, cleaning thoroughly, and reducing equipment loss
- Summary
- Abstract
- Description
- Claims
- Application Information
AI Technical Summary
Problems solved by technology
Method used
Image
Examples
Embodiment 1
[0029] This embodiment provides a water-saving and environmentally friendly production method for chlorinated polyethylene, comprising the steps of:
[0030] 1. Add water to the chlorination reactor;
[0031] 2. Heat the water in the reactor to 60°C, start stirring, and then add polyethylene, magnesium oxide and reaction aids;
[0032] 3. Feed liquid chlorine into the reaction kettle. When the reaction temperature rises from 60°C to 128°C, the mass ratio of chlorine flow is 50%. The remaining liquid chlorine is passed through the 128°C constant temperature section, and the reaction is terminated when the set amount of chlorine flow is reached. Continue to maintain the temperature at 128°C for 5 minutes so that the chlorination reaction can be carried out relatively thoroughly, and cool the material temperature down to 65°C to obtain a chlorinated polyethylene hydrochloric acid suspension;
[0033] 4. Centrifuge and dry the materials in the reactor to obtain chlorinated polyet...
Embodiment 2
[0042] This embodiment provides a water-saving and environmentally friendly production method for chlorinated polyethylene, comprising the steps of:
[0043] 1. Add water to the chlorination reactor;
[0044] 2. Heat the water in the reactor to 60°C, start stirring, and then add polyethylene, magnesium oxide and reaction aids;
[0045] 3. Feed liquid chlorine into the reaction kettle. When the reaction temperature rises from 60°C to 130°C, the mass ratio of chlorine flow is 60%. The remaining liquid chlorine is passed through the 130°C constant temperature section, and the reaction is terminated when the set amount of chlorine flow is reached. Continue to maintain the temperature at 130°C for 30 minutes so that the chlorination reaction is relatively thorough, and cool the material temperature to 60°C to obtain a chlorinated polyethylene hydrochloric acid suspension;
[0046] 4. Centrifuge and dry the materials in the reactor to obtain chlorinated polyethylene and industrial ...
Embodiment 3
[0055] This embodiment provides a water-saving and environmentally friendly production method for chlorinated polyethylene, comprising the steps of:
[0056] 1. Add water to the chlorination reactor;
[0057] 2. Heat the water in the reactor to 60°C, start stirring, and then add polyethylene, magnesium oxide and reaction aids;
[0058] 3. Feed liquid chlorine into the reaction kettle. When the reaction temperature rises from 60°C to 130°C, the mass ratio of chlorine flow is 50%. The remaining liquid chlorine is passed through the 130°C constant temperature section, and the reaction is terminated when the set amount of chlorine flow is reached. Continue to maintain the temperature at 130°C for 30 minutes so that the chlorination reaction is relatively thorough, and cool the material temperature to 60°C to obtain a chlorinated polyethylene hydrochloric acid suspension;
[0059] 4. Centrifuge and dry the materials in the reactor to obtain chlorinated polyethylene and industrial ...
PUM
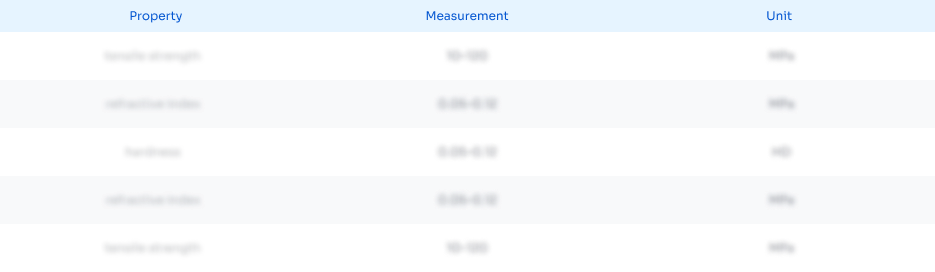
Abstract
Description
Claims
Application Information

- Generate Ideas
- Intellectual Property
- Life Sciences
- Materials
- Tech Scout
- Unparalleled Data Quality
- Higher Quality Content
- 60% Fewer Hallucinations
Browse by: Latest US Patents, China's latest patents, Technical Efficacy Thesaurus, Application Domain, Technology Topic, Popular Technical Reports.
© 2025 PatSnap. All rights reserved.Legal|Privacy policy|Modern Slavery Act Transparency Statement|Sitemap|About US| Contact US: help@patsnap.com