Bonding riveting installation structure of composite top cover used for rail traffic vehicle
A technology for rail transit vehicles and installation structures, applied in the field of lightweight and passive safety of rail transit vehicles, can solve the problems of flat appearance of the roof, poor aesthetics, no passive safety protection function, and inability to achieve vibration reduction effects. The effect of smooth and beautiful surface, light weight and low cost
- Summary
- Abstract
- Description
- Claims
- Application Information
AI Technical Summary
Problems solved by technology
Method used
Image
Examples
Embodiment Construction
[0014] The specific embodiments of the present invention will be further described below in conjunction with the accompanying drawings.
[0015] Such as figure 1 As shown, the riveting installation structure of a composite roof for a rail transit vehicle is a riveting installation structure for a composite roof for a rail transit vehicle, including a composite roof 1, a car body upper suspension beam 2, and a car body upper suspension beam 2 The upper surface of the inner side is a three-level stepped structure, the outer side is a metal profile with unequal sides and right angles, the lower surface of the side is a second-level stepped structure, and the first-level stepped structure on the lower surface of the side of the composite roof 1 is connected with the upper suspension beam 2 of the car body. The two-level stepped structure on the inner upper surface is bonded by sealant 3, and the elastic glue 4 is arranged between the first-level stepped structure on the lower surf...
PUM
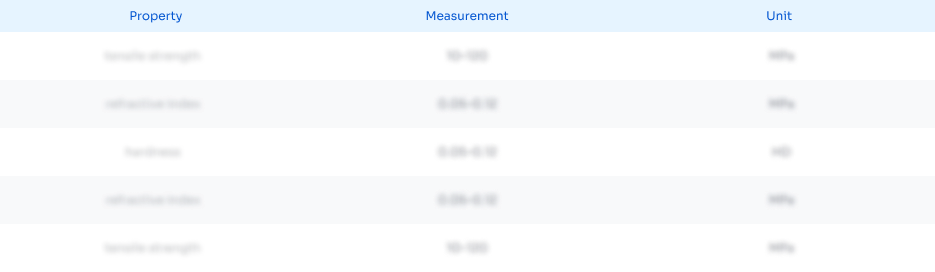
Abstract
Description
Claims
Application Information

- R&D Engineer
- R&D Manager
- IP Professional
- Industry Leading Data Capabilities
- Powerful AI technology
- Patent DNA Extraction
Browse by: Latest US Patents, China's latest patents, Technical Efficacy Thesaurus, Application Domain, Technology Topic, Popular Technical Reports.
© 2024 PatSnap. All rights reserved.Legal|Privacy policy|Modern Slavery Act Transparency Statement|Sitemap|About US| Contact US: help@patsnap.com