Spinning method of multi-component blended yarns based on compact spinning
A technology of blended yarn and compact spinning, which is applied in the direction of yarn, textiles and papermaking, etc. It can solve the problems that affect the enthusiasm for investment in compact spinning technology, restrict the development of compact spinning technology production, increase energy consumption and machine material consumption, and achieve improvement. High-end wearing function, delicate and soft hand feeling, cost reduction effect
- Summary
- Abstract
- Description
- Claims
- Application Information
AI Technical Summary
Problems solved by technology
Method used
Examples
Embodiment 1
[0015] A kind of spinning method of multi-component blended yarn based on compact spinning, comprising: selection of raw materials, jute fiber 18%, spun silk fiber 26%, hemp fiber 19%, apocynum fiber 26% by weight, aloe fiber 9%, tencel fiber 8%; the production process configuration, jute fiber, spun silk fiber, hemp fiber, apocynum, aloe fiber, tencel fiber respectively adopt the existing equipment FA002A disc plucking machine, ZFA036 mixed Cotton opener, FA022-6 multi-compartment blending machine, ZF1102A card needle opener, FA046A vibrating cotton box feeder, FA141A single beater lapping machine, FA224D carding machine, JWF1310 drawing frame unpacking and mixing into sliver; Jute fiber, spun silk fiber, hemp fiber, apocynum fiber, aloe fiber, tencel fiber drawing mixing and spinning, respectively use JWF1310 drawing frame, KSB-D22C drawing frame pre-drawing, three-way mixing Draw frame, use FA497 roving frame, JWF1510 spinning frame, SAV10 winding machine to spin; determine...
Embodiment 2
[0017] Raw material selection, fiber selection 12% jute fiber, 15% spun silk fiber, 25% hemp fiber, 30% weight portion of apocynum fiber, 10% aloe fiber, 10% tencel fiber, production process configuration, jute fiber, Spun silk fiber, hemp fiber, apocynum, aloe fiber, and tencel fiber respectively use the existing equipment FA002A disc plucking machine, ZFA036 mixed cotton opener, FA022-6 multi-compartment mixed cotton machine, ZF1102A card needle opener Cotton machine, FA046A vibrating cotton box feeder, FA141A single hand lapping machine, FA224D carding machine, JWF1310 drawing frame unpacking and mixing into strips; jute fiber, spun silk fiber, hemp fiber, apocynum fiber, aloe vera Drawing, mixing and spinning of fibers and Tencel fibers, respectively using JWF1310 drawing frame, KSB-D22C drawing frame for pre-drawing, three-way mixed drawing, using FA497 roving frame, JWF1510 spinning frame, SAV10 winding machine for spinning Yarn; determine the main parameters. In the ope...
Embodiment 3
[0019]Raw material selection Fiber selection jute fiber 20%, silk fiber 28%, hemp fiber 28%, apocynum fiber 30% by weight, aloe fiber 9%, tencel fiber 9%. Production process configuration, jute fiber, spun silk fiber, hemp fiber, apocynum fiber, aloe fiber, tencel fiber respectively adopt the existing equipment FA002A disc plucking machine, ZFA036 mixed cotton opener, FA022-6 multi-storey Cotton blending machine, ZF1102A card opening machine, FA046A vibrating cotton box feeder, FA141A single hand lapping machine, FA224D carding machine, JWF1310 drawing frame unpacking and mixing into strips; jute fiber, spun silk fiber, hemp The drawing, blending and spinning of Aloe fiber, apocynum fiber, aloe fiber and tencel fiber, respectively using JWF1310 drawing frame, KSB-D22C drawing frame for pre-drawing, and three-way mixing and drawing, using FA497 roving frame and JWF1510 Spinning frame and SAV10 winder; determine the main parameters. In the opening and cleaning process, the volum...
PUM
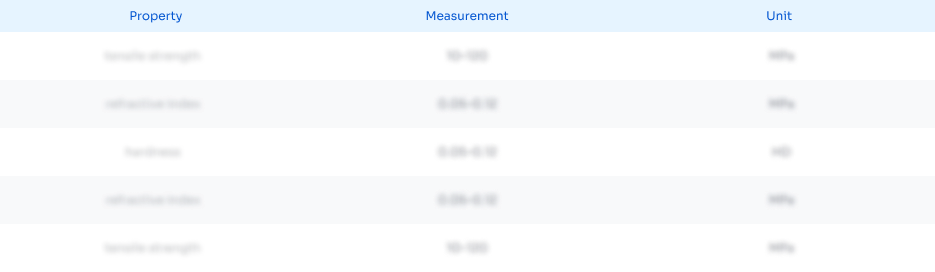
Abstract
Description
Claims
Application Information

- Generate Ideas
- Intellectual Property
- Life Sciences
- Materials
- Tech Scout
- Unparalleled Data Quality
- Higher Quality Content
- 60% Fewer Hallucinations
Browse by: Latest US Patents, China's latest patents, Technical Efficacy Thesaurus, Application Domain, Technology Topic, Popular Technical Reports.
© 2025 PatSnap. All rights reserved.Legal|Privacy policy|Modern Slavery Act Transparency Statement|Sitemap|About US| Contact US: help@patsnap.com