Resonance-peak-free shock absorber with built-in negative-stiffness dynamic vibration absorber
A technology of dynamic shock absorber and negative stiffness, which is applied in the direction of spring/shock absorber functional characteristics, spring/shock absorber, vibration suppression adjustment, etc. Difficult, large negative stiffness and other problems, to achieve the effect of compact structure, small mass and simple principle
- Summary
- Abstract
- Description
- Claims
- Application Information
AI Technical Summary
Problems solved by technology
Method used
Image
Examples
Embodiment 1
[0028] Such as figure 1 As shown, the non-resonance peak shock absorber of the present invention embedded with a single set of disc spring negative stiffness dynamic shock absorbers is composed of the following parts: an upper connector 1, an elastic element 2, a lower connector 3, a dynamic shock absorber and a single set disc spring 6.
[0029] The upper connecting piece 1 is located at the top of the whole device and has an axisymmetric structure, the inner concave surface of the side is arc-shaped, and the bottom surface is a plane;
[0030] The elastic element 2 is located under the upper connecting piece 1 and has an axisymmetric structure. The upper surface of the elastic element 2 is in close contact with the concave arc-shaped side surface of the upper connecting piece 1, and the lower surface is inclined upward; The elastic element 2 provides vibration isolation;
[0031] The lower connecting part 3 is located under the elastic element 2, and has a symmetrical stru...
Embodiment 2
[0041] Embodiment 2 of the present invention is as figure 2 shown. The single group of disc springs in Embodiment 1 is modified into multiple groups of disc springs arranged symmetrically around the circumference, and the rest of the components are the same as those in Embodiment 1. The use of multiple sets of disc springs in this embodiment can ensure that the mass block vibrates along the vertical direction, and at the same time can enhance the stability of the support, and the synergistic effect of multiple sets of disc springs can obtain more stable negative stiffness characteristics.
[0042] Such as image 3 As shown, the upper connecting piece 1 and the lower connecting piece 3 are equivalent to the approximately rigid black shaded part, and the elastic element 2 is equivalent to the spring k s , bellows 4 and mass block 5 are equivalent to spring k e and damping c, disc spring 6 is equivalent to negative stiffness k n (k n 2 xn x<0, so the inertial force of the m...
PUM
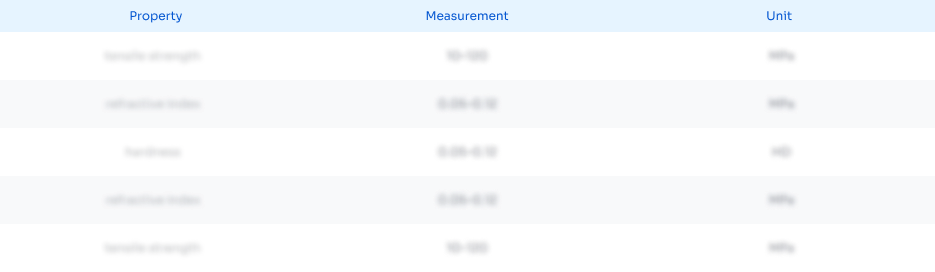
Abstract
Description
Claims
Application Information

- R&D
- Intellectual Property
- Life Sciences
- Materials
- Tech Scout
- Unparalleled Data Quality
- Higher Quality Content
- 60% Fewer Hallucinations
Browse by: Latest US Patents, China's latest patents, Technical Efficacy Thesaurus, Application Domain, Technology Topic, Popular Technical Reports.
© 2025 PatSnap. All rights reserved.Legal|Privacy policy|Modern Slavery Act Transparency Statement|Sitemap|About US| Contact US: help@patsnap.com