Processing method of low temperature resistant and oil resistant rubber sealing ring
A technology of rubber sealing ring and processing method, which is applied in the processing field of low temperature and oil resistant rubber sealing ring, can solve the problems that the seal is difficult to maintain elasticity and sealing performance, and the low temperature resistance performance is reduced, so as to improve the mechanical properties and enhance the low temperature resistance. performance and compression set resistance, the effect of good mechanical properties
- Summary
- Abstract
- Description
- Claims
- Application Information
AI Technical Summary
Problems solved by technology
Method used
Image
Examples
Embodiment 1
[0037] (1) Batching: take the raw materials of the following parts by weight, and obtain the rubber compound after being mixed by a high-speed mixer;
[0038] Nitrile rubber (acrylonitrile content is 31-35wt%) 60kg, rare earth butadiene rubber BR Nd40 10kg, kaolin 5kg, sepiolite powder 5kg, ultrafine polytetrafluoroethylene powder 2kg, C5 hydrogenated petroleum resin 2kg, accelerator TiBTM 0.5kg, anti-aging agent 44PD 0.5kg, anti-reversion agent Perkalink900 0.5kg, lubricant calcium stearate 0.5kg;
[0039] (2) Mixing: The mixing process is divided into two stages. In the first stage, the mixing temperature is 110-120°C, the mixing speed is 120r / min, and the mixing time is 10min. The cooling speed is cooled to 20-30°C and kept for 3 hours, the second stage mixing temperature is 140-150°C, mixing speed is 120r / min, and mixing time is 10min;
[0040] (3) Vulcanization: Extrude the kneaded rubber material into molding, then inject the molded film into the mold of the vulcanizer,...
Embodiment 2
[0045] (1) Batching: take the raw materials of the following parts by weight, and obtain the rubber compound after being mixed by a high-speed mixer;
[0046]Nitrile rubber (acrylonitrile content is 31-35wt%) 70kg, rare earth butadiene rubber BR Nd40 10kg, kaolin 5kg, sepiolite powder 5kg, ultrafine polytetrafluoroethylene powder 3kg, C5 hydrogenated petroleum resin 2kg, accelerator TiBTM 0.5kg, anti-aging agent 44PD 0.5kg, anti-reversion agent Perkalink900 0.5kg, lubricant calcium stearate 0.5kg;
[0047] (2) Mixing: The mixing process is divided into two stages. In the first stage, the mixing temperature is 110-120°C, the mixing speed is 120r / min, and the mixing time is 10min. The cooling speed is cooled to 20-30°C and kept for 3 hours, the second stage mixing temperature is 140-150°C, mixing speed is 120r / min, and mixing time is 10min;
[0048] (3) Vulcanization: Extrude the kneaded rubber material into molding, then inject the molded film into the mold of the vulcanizer, ...
Embodiment 3
[0053] (1) Batching: take the raw materials of the following parts by weight, and obtain the rubber compound after being mixed by a high-speed mixer;
[0054] Nitrile rubber (acrylonitrile content is 31-35wt%) 70kg, rare earth butadiene rubber BR Nd40 10kg, kaolin 5kg, sepiolite powder 5kg, ultrafine polytetrafluoroethylene powder 3kg, C5 hydrogenated petroleum resin 2kg, accelerator TiBTM 0.5kg, anti-aging agent 44PD 0.5kg, anti-reversion agent Perkalink900 0.5kg, lubricant 0.5kg;
[0055] (2) Mixing: The mixing process is divided into two stages. In the first stage, the mixing temperature is 110-120°C, the mixing speed is 120r / min, and the mixing time is 10min. The cooling speed is cooled to 20-30°C and kept for 3 hours, the second stage mixing temperature is 140-150°C, mixing speed is 120r / min, and mixing time is 10min;
[0056] (3) Vulcanization: Extrude the kneaded rubber material into molding, then inject the molded film into the mold of the vulcanizer, and vulcanize un...
PUM
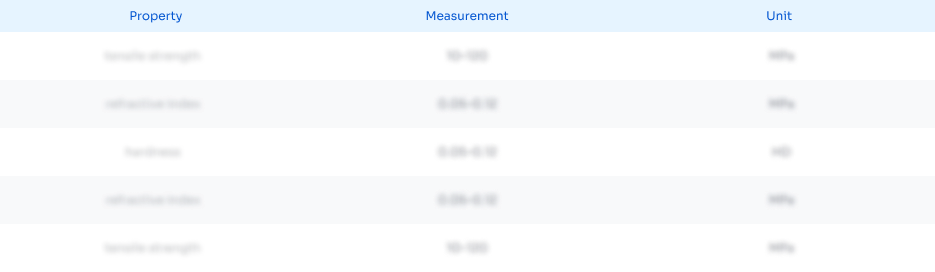
Abstract
Description
Claims
Application Information

- R&D Engineer
- R&D Manager
- IP Professional
- Industry Leading Data Capabilities
- Powerful AI technology
- Patent DNA Extraction
Browse by: Latest US Patents, China's latest patents, Technical Efficacy Thesaurus, Application Domain, Technology Topic, Popular Technical Reports.
© 2024 PatSnap. All rights reserved.Legal|Privacy policy|Modern Slavery Act Transparency Statement|Sitemap|About US| Contact US: help@patsnap.com