Preparation method of 4-aminobutanol
A technology of aminobutanol and chlorobutanol, which is applied to the preparation of aminohydroxyl compounds, the preparation of organic compounds, chemical instruments and methods, etc., which can solve the problems of unsuitable large-scale industrial production, harsh preparation conditions, and natural safety hazards of catalysts, etc. problems, to achieve the effects of large-scale industrial production, simple and easy post-processing, and significant social and economic benefits
- Summary
- Abstract
- Description
- Claims
- Application Information
AI Technical Summary
Problems solved by technology
Method used
Image
Examples
Embodiment 1
[0029] (1) Add 74.08g phthalimide potassium salt, 500ml dimethylformamide, 0.7g tetrabutylammonium bromide in a three-necked flask with a volume of 1L, mix and stir to obtain the mixture, and then pour it under room temperature 52.13 g of 4-chlorobutanol was added dropwise into the mixture (stirring while adding, the dropwise addition was completed in 0.5 h), and after the dropwise addition was completed, the reaction was completed by stirring at 80°C for 9 h to obtain a mixed solution of the intermediate;
[0030] Then, under the action of the water pump, the mixed solution of the intermediate was subjected to rotary evaporation, and the dimethylformamide was removed by evaporation. After the evaporation was completed, 300ml of dichloromethane was added to the remaining product and mixed and stirred evenly to obtain the intermediate. Dichloromethane solution; Then first use the sodium hydroxide solution that mass concentration is 2% to the dichloromethane solution washing extr...
Embodiment 2
[0038] (1) Add 74.08g phthalimide potassium salt, 500ml dimethyl sulfoxide, 0.7g hexadecyldimethylammonium bromide in a three-necked flask with a volume of 1L, mix and stir to obtain a mixture, Then, 52.13g of 4-chlorobutanol was added dropwise to the mixture at room temperature (stirring while adding, and the dropwise addition was completed in 0.5h). mixture;
[0039] Then under the effect of water pump, the mixed solution of the intermediate is subjected to rotary evaporation, and the dimethyl sulfoxide is removed by evaporation. After the evaporation is completed, 300ml of dichloromethane is added to the remaining product and mixed and stirred to obtain the intermediate. Dichloromethane solution; Then first use the sodium hydroxide solution that mass concentration is 2% to the dichloromethane solution washing extraction of intermediate twice (each with 100ml), then wash and extract once with 100ml saturated sodium chloride solution, Wash the organic phase obtained after th...
Embodiment 3
[0047] (1) Add 74.08g phthalimide potassium salt, 500ml dimethyl sulfoxide, 0.7g hexadecyldimethylammonium bromide in a three-necked flask with a volume of 1L, mix and stir to obtain a mixture, Then, 56.47g of 4-chlorobutanol was added dropwise to the mixture at room temperature (stirring while adding, and the dropwise addition was completed in 0.5h). mixture;
[0048] Then under the effect of water pump, the mixed solution of the intermediate is subjected to rotary evaporation, and the dimethyl sulfoxide is removed by evaporation. After the evaporation is completed, 300ml of dichloromethane is added to the remaining product and mixed and stirred to obtain the intermediate. Dichloromethane solution; Then first use the sodium hydroxide solution that mass concentration is 2% to the dichloromethane solution washing extraction of intermediate twice (each with 100ml), then wash and extract once with 100ml saturated sodium chloride solution, Wash the organic phase obtained after th...
PUM
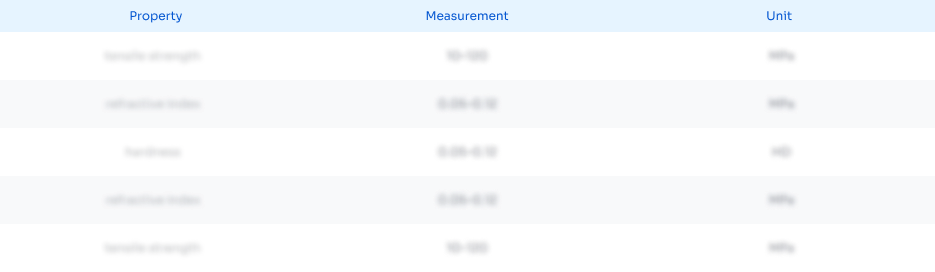
Abstract
Description
Claims
Application Information

- R&D
- Intellectual Property
- Life Sciences
- Materials
- Tech Scout
- Unparalleled Data Quality
- Higher Quality Content
- 60% Fewer Hallucinations
Browse by: Latest US Patents, China's latest patents, Technical Efficacy Thesaurus, Application Domain, Technology Topic, Popular Technical Reports.
© 2025 PatSnap. All rights reserved.Legal|Privacy policy|Modern Slavery Act Transparency Statement|Sitemap|About US| Contact US: help@patsnap.com