Multifunctional bionic mechanical pincer with autonomously-distributed power
A bionic machinery and multi-functional technology, applied in the field of bionic robots, can solve the problems of long charging time, single movement mode, wear and tear of connecting cables, etc., to improve the reliability of the whole machine, facilitate installation and disassembly, and reduce wear and tear failures.
- Summary
- Abstract
- Description
- Claims
- Application Information
AI Technical Summary
Problems solved by technology
Method used
Image
Examples
Embodiment 1
[0033] refer to figure 1 , figure 2 In this embodiment, the multifunctional bionic mechanical pincers with autonomously distributed power mainly include a connecting frame 1, a three-dimensional joint 2, a pincer joint A, a two-dimensional joint I3, a pincer shield joint C, a power device 5, an electric control device 6, a chain Saw 8; the three-dimensional joint 2 is fixed on the connecting frame 1 and connected with the claw joint A, the claw joint A is connected with the claw-shield joint C through the two-dimensional joint I3, the chain saw 8 is fixed on the claw-shield joint C, and the power device 5 mainly includes The battery pack I501 and the battery pack II502 are respectively fixed in the cavities of the claw joint A and the claw-shield joint C, and the electric control device 6 is fixed in the cavity of the claw-shield joint C, and the electric control device 6 is respectively connected with the power device 5 and the three-dimensional joint 2 , Two-dimensional jo...
Embodiment 2
[0040] refer to image 3 , Figure 4 In this embodiment, the multifunctional bionic mechanical pliers with autonomously distributed power includes a connecting frame 1, a three-dimensional joint 2, a claw joint A, a two-dimensional joint I3, a claw joint B, a two-dimensional joint II4, a claw-shield joint C, and a forceps motion Mechanism 7, clamp D, power device 5, electric control device 6, circular saw 8; three-dimensional joint 2 is fixed on the connecting frame 1 and connected with claw A, and claw A is connected with claw B through two-dimensional joint I3, Claw segment B is connected to the claw segment C through the two-dimensional joint II4, and the claw segment C is connected to the clamp segment D through the clamp mechanism 7. The power unit 5 mainly includes a battery pack I501 and a battery pack II502, which are respectively fixed on the claw segment B and the clamp segment D. In the cavity of the chelicer-shield segment C, the electric control device 6 is fixed...
Embodiment 3
[0047] refer to Figure 5 , Figure 6 , in this embodiment, the difference between the multifunctional bionic mechanical pincers with autonomously distributed power and that of Embodiment 2 is only that:
[0048] The power device is a hydraulic power system, and the battery pack has only one battery pack I501, which also includes a drive motor 503, a hydraulic pump 504, a miniature oil tank 505, and a hydraulic solenoid valve group 506; the drive motor 503, hydraulic pump 504, and miniature oil tank 505 are connected in sequence Fixed in the cavity of claw-shield section C, hydraulic solenoid valve group 506 is fixed in the cavity of claw section B, and connected with hydraulic pump 504 through hydraulic pipelines; battery pack I 501 is fixed in the cavity of claw section A, and It is electrically connected with the drive motor 503; the electric control device 6 includes a controller 601, a charging port 602, an electrical plug-in 603, and a pressure sensor 604; the controlle...
PUM
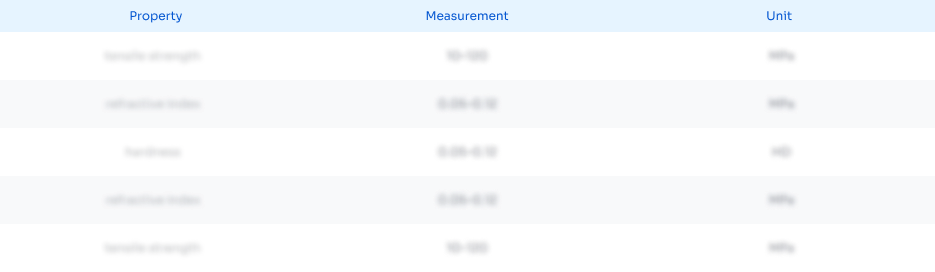
Abstract
Description
Claims
Application Information

- R&D Engineer
- R&D Manager
- IP Professional
- Industry Leading Data Capabilities
- Powerful AI technology
- Patent DNA Extraction
Browse by: Latest US Patents, China's latest patents, Technical Efficacy Thesaurus, Application Domain, Technology Topic, Popular Technical Reports.
© 2024 PatSnap. All rights reserved.Legal|Privacy policy|Modern Slavery Act Transparency Statement|Sitemap|About US| Contact US: help@patsnap.com