Current sensor based on auto-bias magnetoelectric composite material
A magnetoelectric composite material and current sensor technology, applied in the direction of measuring current/voltage, instruments, measuring devices, etc., can solve the problems of complex sensor structure, unadjustable resonance frequency, unfavorable miniaturization, etc., and achieve small size, high sensitivity, Favorable effect of miniaturization
- Summary
- Abstract
- Description
- Claims
- Application Information
AI Technical Summary
Problems solved by technology
Method used
Image
Examples
Embodiment Construction
[0020] The present invention will be further described below in conjunction with the accompanying drawings, wherein the same structures are named with the same names. In describing the present invention, it should be understood that the terms "upper", "lower", "front", "rear", "left", "right", "top", "bottom", "inner", " The orientation or positional relationship indicated by "outside", etc. is based on the orientation or positional relationship shown in the drawings, and is only for the convenience of describing the present invention and simplifying the description, rather than indicating or implying that the referred device or element must have a specific orientation, so as to Specific orientation configurations and operations, therefore, are not to be construed as limitations on the invention.
[0021] Such as figure 1 with figure 2 As shown, a current sensor based on a self-biased magnetoelectric composite material is composed of a support base 1, a packaging shell 2, a...
PUM
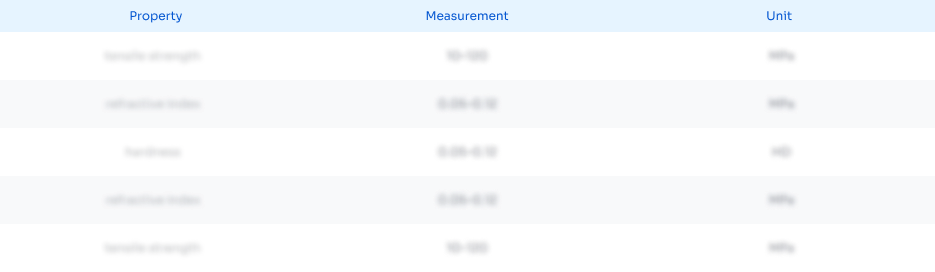
Abstract
Description
Claims
Application Information

- R&D
- Intellectual Property
- Life Sciences
- Materials
- Tech Scout
- Unparalleled Data Quality
- Higher Quality Content
- 60% Fewer Hallucinations
Browse by: Latest US Patents, China's latest patents, Technical Efficacy Thesaurus, Application Domain, Technology Topic, Popular Technical Reports.
© 2025 PatSnap. All rights reserved.Legal|Privacy policy|Modern Slavery Act Transparency Statement|Sitemap|About US| Contact US: help@patsnap.com