Microfiber synthetic leather dyeing technology aimed at improving dye uptake and color fastness
A technology of superfine fiber and synthetic leather, applied in the field of synthetic leather dyeing, can solve the problems of polyamide superfine fiber dyeing performance difference, inability to obtain dyeing effect, poor color fastness of products, etc., to enhance color fastness to washing, improve Dyeing aid effect, effect of improving dye uptake rate
- Summary
- Abstract
- Description
- Claims
- Application Information
AI Technical Summary
Problems solved by technology
Method used
Examples
Embodiment 1
[0025] (1) Low temperature and high pressure treatment of natto gum: 50g of water-treatment grade natto gum was added to the autoclave, and water was added to make the water content reach 45wt%, and nitrogen was used to replace the air in the autoclave and continue to feed nitrogen to make the pressure in the autoclave reach 45% by weight. 2MPa, and heat up to make the temperature in the kettle reach 50°C, keep stirring for 10 minutes, continue to feed nitrogen to make the pressure in the kettle reach 3MPa, heat up again to make the temperature in the kettle reach 65°C, keep stirring for 5 minutes, stop feeding nitrogen, and discharge the obtained paste body, and then the paste is sent to a freeze dryer, and the solid obtained by drying is made into micropowder by an ultrafine pulverizer;
[0026] (2) Preparation of auxiliary materials: fully mix 2g sodium lauroyl glutamate and 2.5g dodecyl glucoside to make granules by dry granulation, and then make micropowders through ultraf...
Embodiment 2
[0031] (1) Low temperature and high pressure treatment of natto gum: 50g of water-treatment grade natto gum was added to the autoclave, and water was added to make the water content reach 45wt%, and nitrogen was used to replace the air in the autoclave and continue to feed nitrogen to make the pressure in the autoclave reach 45% by weight. 2MPa, and heat up to make the temperature in the kettle reach 50°C, keep stirring for 10 minutes, continue to feed nitrogen to make the pressure in the kettle reach 3MPa, heat up again to make the temperature in the kettle reach 65°C, keep stirring for 5 minutes, stop feeding nitrogen, and discharge the obtained paste body, and then the paste is sent to a freeze dryer, and the solid obtained by drying is made into micropowder by an ultrafine pulverizer;
[0032] (2) Preparation of auxiliary materials: fully mix 2.5 g of sodium lauroyl glutamate and 2 g of dodecyl glucoside to make granules by dry granulation, and then use an ultrafine pulveri...
Embodiment 3
[0037] (1) Low temperature and high pressure treatment of natto gum: 50g of water-treatment grade natto gum was added to the autoclave, and water was added to make the water content reach 45wt%, and nitrogen was used to replace the air in the autoclave and continue to feed nitrogen to make the pressure in the autoclave reach 45% by weight. 2MPa, and heat up to make the temperature in the kettle reach 50°C, keep stirring for 10 minutes, continue to feed nitrogen to make the pressure in the kettle reach 3MPa, heat up again to make the temperature in the kettle reach 65°C, keep stirring for 5 minutes, stop feeding nitrogen, and discharge the obtained paste body, and then the paste is sent to a freeze dryer, and the solid obtained by drying is made into micropowder by an ultrafine pulverizer;
[0038] (2) Preparation of excipients: 2.5g sodium lauroyl glutamate, 2.5g nano-gel powder and 2g dodecyl glucoside are fully mixed, then dry granulated to make granules, and then ultrafine p...
PUM
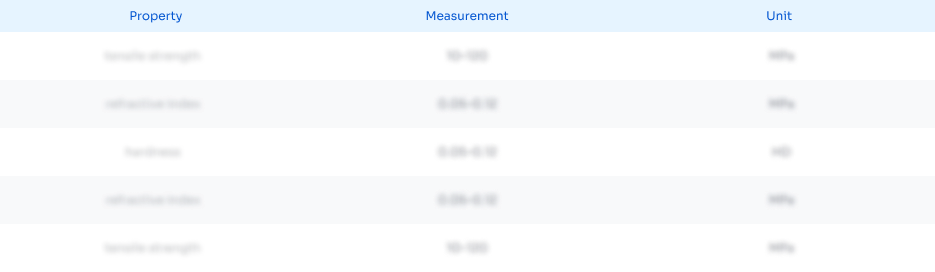
Abstract
Description
Claims
Application Information

- Generate Ideas
- Intellectual Property
- Life Sciences
- Materials
- Tech Scout
- Unparalleled Data Quality
- Higher Quality Content
- 60% Fewer Hallucinations
Browse by: Latest US Patents, China's latest patents, Technical Efficacy Thesaurus, Application Domain, Technology Topic, Popular Technical Reports.
© 2025 PatSnap. All rights reserved.Legal|Privacy policy|Modern Slavery Act Transparency Statement|Sitemap|About US| Contact US: help@patsnap.com