Method for synthesizing biphenyldianhydride in continuous flow microchannel reactor
A technology of microchannel reactor and channel reactor, which is applied in organic chemistry, chemical recycling, etc., can solve the problems of low product consistency, high equipment cost, and low consistency, and achieve energy utilization rate improvement, easy maintenance, and consistent sex enhancing effect
- Summary
- Abstract
- Description
- Claims
- Application Information
AI Technical Summary
Problems solved by technology
Method used
Image
Examples
Embodiment 1
[0031] Add 100kg of 2,2', 3,3'-tetramethylbiphenyl and 400kg of glacial acetic acid into the mixing kettle, and add 600g of cobalt acetate, 400g of manganese acetate and 500g of tetrabromoethane into the kettle, stir and mix evenly and preheat Tetramethylbiphenyl dissolves. The mixed liquid is pumped into the microchannel reactor through the feed pump, and oxygen is introduced at the same time, and the oxygen amount: tetramethylbiphenyl molar ratio is 8:1. The reaction pressure is controlled at 1.5MPa, the temperature is 200°C, and the reaction time of the reactants in the microchannel reactor is 45s. After cooling, the oxidized product is transferred to the receiving tank for separation. After cooling, the tetraacid is precipitated, filtered and washed. 3,3'-biphenyldianhydride was prepared by melting and heating dehydration, with a comprehensive yield of 92%. Acetic acid can be reused through refining, and the residue can be refined to recover the catalyst.
Embodiment 2
[0033]Add 42kg of 2,3', 3,4'-tetramethylbis, 130kg of glacial acetic acid into the mixing kettle, and add 35g of cobalt acetate, 70g of manganese acetate and 110g of tetrabromoethane into the kettle, stir and mix evenly and preheat to Tetramethylbiphenyl dissolves. The mixed liquid is pumped into the microchannel reactor through the feed pump, and oxygen is introduced at the same time, and the amount of oxygen: the amount of chlorinated o-xylene is 10:1. The reaction pressure is controlled at 2.5MPa, the temperature is 180°C, and the reaction time of the reactants in the microchannel reactor is 80s. After cooling, the oxidized product is transferred to the receiving tank for separation. After cooling, the tetraacid is precipitated, filtered and washed. 3,3'-biphenyldianhydride was prepared by melting and heating dehydration with a comprehensive yield of 92.6%. Acetic acid can be reused through refining, and the residue can be refined to recover the catalyst.
Embodiment 3
[0035] 21kg of 2,2', 3,3'-tetramethylbiphenyl, 2,3', 3,4'-tetramethylbiphenyl, 3,3', 4,4'-tetramethylbiphenyl The mixture, 84kg of glacial acetic acid was added to the mixing kettle, and 200g of cobalt acetate, 200g of manganese acetate, and 100g of tetrabromoethane were added to the kettle, and stirred and mixed evenly. And the mixed solution is pumped into the microchannel reactor through the feed pump, and oxygen is introduced at the same time, and the ratio of the molar amount of oxygen to the amount of chlorinated o-xylene is 6.5:1. The reaction pressure is controlled at 1.25MPa, the temperature is 300°C, and the reaction time of the reactants in the microchannel reactor is 50s. After cooling, the oxidized product is transferred to a receiving tank for gas-liquid separation, and the acetic acid is removed by flash evaporation, and the remaining product is subjected to vacuum distillation to obtain mixed biphenyldianhydride. The comprehensive yield of this embodiment is 8...
PUM
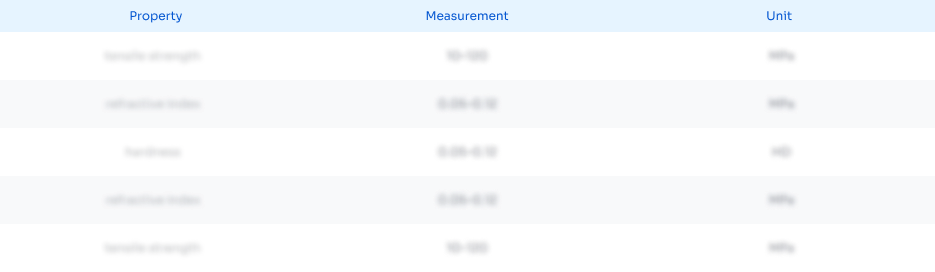
Abstract
Description
Claims
Application Information

- Generate Ideas
- Intellectual Property
- Life Sciences
- Materials
- Tech Scout
- Unparalleled Data Quality
- Higher Quality Content
- 60% Fewer Hallucinations
Browse by: Latest US Patents, China's latest patents, Technical Efficacy Thesaurus, Application Domain, Technology Topic, Popular Technical Reports.
© 2025 PatSnap. All rights reserved.Legal|Privacy policy|Modern Slavery Act Transparency Statement|Sitemap|About US| Contact US: help@patsnap.com