Direct-drive transmission mechanism
A transmission mechanism and direct drive technology, applied in the direction of electromechanical devices, structural connections, electric components, etc., can solve the problems of repeated positioning accuracy and poor positioning accuracy, large section width, cumulative error of mechanical parts, ball screw backlash error, etc. Achieve the effect of eliminating backlash error and reducing cost
- Summary
- Abstract
- Description
- Claims
- Application Information
AI Technical Summary
Problems solved by technology
Method used
Image
Examples
Embodiment 1
[0019] Such as figure 1 As shown, this embodiment includes a base 1, a guide rail 3 is provided on the top surface of the base 1, a slide seat 4 is provided on the guide rail 3 to move along the guide rail, the slide seat 4 is fixed with a mover coil assembly 6 by screws, and the base side is provided with The stator permanent magnet 7, the mover coil assembly 6 corresponds to the stator permanent magnet 7, and there is an air gap between the two. The non-contact transmission of the mover coil assembly 6 and the stator permanent magnet 7 can avoid mechanical wear and tear during movement. Backlash, high reliability, long life;
[0020] Corresponding to the guide rail 3, this embodiment is provided with a magnetic scale 2 parallel to it, and the slide 4 is provided with a reading head 5 corresponding to the magnetic scale 2, and real-time feedback is performed through the high-resolution position detection of the magnetic scale 2 and the reading head 5 , to achieve full closed...
Embodiment 2
[0027] Such as figure 2 As shown, the difference between this embodiment and Embodiment 1 is that the guide rails 3 are double row guide rails, which are arranged on both sides of the base 1, one of the guide rails 3 is paired with a magnetic scale 2, and the slide seat 4 adopts U-shaped structure, the mover coil assembly 6 is directly potted in the sliding seat 4, the stator permanent magnet 7 is arranged on the top surface of the base 1, the mover coil assembly 6 and the stator permanent magnet 7 are placed in parallel, and an air gap is ensured. The positions of the limit block 8, the hard limit seat 9 and the reading head 5 change accordingly.
[0028] The double-row guide rails have a symmetrical structure, have higher rigidity, and can bear larger loads.
Embodiment 3
[0030] Such as image 3 As shown, the difference between this embodiment and Embodiment 1 is that the guide rail 3 and the magnetic scale 2 are arranged on one side of the base 1, the stator permanent magnet 7 is arranged on the top surface of the base 1, and the mover coil assembly 6 is set on the corresponding installation surface of the sliding seat 4, placed parallel to the stator permanent magnet 7, and ensures the air gap. The positions of the limit block 8, the hard limit seat 9 and the reading head 5 change accordingly.
PUM
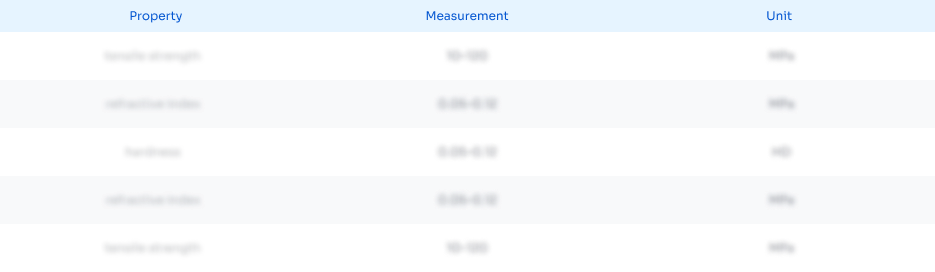
Abstract
Description
Claims
Application Information

- R&D
- Intellectual Property
- Life Sciences
- Materials
- Tech Scout
- Unparalleled Data Quality
- Higher Quality Content
- 60% Fewer Hallucinations
Browse by: Latest US Patents, China's latest patents, Technical Efficacy Thesaurus, Application Domain, Technology Topic, Popular Technical Reports.
© 2025 PatSnap. All rights reserved.Legal|Privacy policy|Modern Slavery Act Transparency Statement|Sitemap|About US| Contact US: help@patsnap.com