Heat treatment method for roller cone
A heat treatment method and roller cone technology, applied in heat treatment furnaces, heat treatment equipment, coatings, etc., can solve the problems of carburized layer and uneven hardness, large deformation of the inner hole of the roller cone, affecting the service life, etc. and uniform hardness, improve carburizing quality, and benefit the organization
- Summary
- Abstract
- Description
- Claims
- Application Information
AI Technical Summary
Problems solved by technology
Method used
Image
Examples
Embodiment 1
[0045] The material of the cone is 15MnNi4Mo, including the following chemical composition in mass fraction Wt%: C 0.14%, Cr 0.18%, Ni 3.35%, Mo 0.36%, Si 0.28%, Mn 0.86%, S 0.004% and P 0.011%.
[0046] The gear manufacturing process is rough machining → carburizing, high temperature tempering → semi-finishing machining → quenching, low temperature tempering → finishing machining.
[0047] In this embodiment, carburizing and quenching are completed in a heat treatment carburizing and quenching multipurpose furnace; high-temperature tempering and low-temperature tempering are respectively completed in a high-temperature tempering furnace and a low-temperature tempering furnace. The specific steps are:
[0048] 1) Carburizing: Carburize the cone preform into the front chamber of the multi-purpose furnace, the temperature is controlled at 925°C, the strong infiltration period is 900 minutes, the carbon potential is 1.25%, the diffusion period is 240 minutes, the carbon potential...
Embodiment 2
[0062] The material of the cone is 15MnNi4Mo, including the following chemical composition in mass fraction Wt%: C 0.14%, Cr 0.18%, Ni 3.35%, Mo 0.36%, Si 0.28%, Mn 0.86%, S 0.004% and P 0.011%.
[0063] The embodiment of the present invention is used for the heat treatment method of cone, comprises the following steps:
[0064] 1) Carburizing: put the cone into the front chamber of the multi-purpose furnace for carburizing, the temperature is controlled at 930°C, the strong infiltration period is 850 minutes, the carbon potential is 1.3%, the diffusion period is 250 minutes, and the carbon potential is 1.2%. After the diffusion period is completed, Lower the temperature to 840°C and enter the back room to cool slowly to 460°C and leave the oven;
[0065] 2) High-temperature tempering: Put the cones that are slowly cooled after carburizing into the high-temperature tempering furnace, and the temperature is controlled at 690°C. After tempering for 10 hours under the protection ...
Embodiment 3
[0078] The material of the cone is 15MnNi4Mo, including the following chemical composition in mass fraction Wt%: C 0.14%, Cr 0.18%, Ni 3.35%, Mo 0.36%, Si 0.28%, Mn 0.86%, S 0.004% and P 0.011%.
[0079] The embodiment of the present invention is used for the heat treatment method of cone, comprises the following steps:
[0080] 1) Carburizing: put the cone into the front chamber of the multi-purpose furnace for carburizing, the temperature is controlled at 925-928°C, the strong infiltration period is 950 minutes, the carbon potential is 1.2%, the diffusion period is 230 minutes, the carbon potential is 0.95%, and the diffusion period is completed Afterwards, the temperature is lowered to 850°C and then slowly cooled to 430°C in the back room;
[0081] 2) High-temperature tempering: Put the cones that have been slowly cooled after carburizing into a high-temperature tempering furnace, and the temperature is controlled at 670°C. After tempering for 14 hours under the protection...
PUM
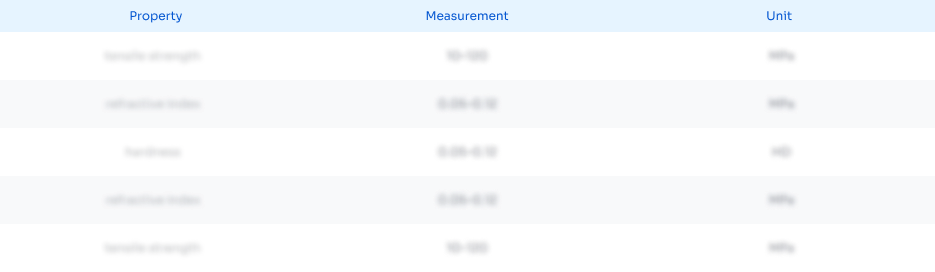
Abstract
Description
Claims
Application Information

- R&D Engineer
- R&D Manager
- IP Professional
- Industry Leading Data Capabilities
- Powerful AI technology
- Patent DNA Extraction
Browse by: Latest US Patents, China's latest patents, Technical Efficacy Thesaurus, Application Domain, Technology Topic, Popular Technical Reports.
© 2024 PatSnap. All rights reserved.Legal|Privacy policy|Modern Slavery Act Transparency Statement|Sitemap|About US| Contact US: help@patsnap.com