A three-degree-of-freedom ultrasonic vibration-assisted machining precision positioning platform
A technology of ultrasonic vibration and precise positioning, which is applied in the direction of machines/supports, supporting machines, mechanical equipment, etc., can solve the problems of few ultrasonic vibration-assisted processing platforms, cannot meet processing requirements, and cannot realize three-dimensional processing, etc., and achieves compact structure, Effect of reducing assembly and preventing damage
- Summary
- Abstract
- Description
- Claims
- Application Information
AI Technical Summary
Problems solved by technology
Method used
Image
Examples
Embodiment Construction
[0018] In order to further understand the invention content, characteristics and effects of the present invention, the following examples are given, and detailed descriptions are as follows in conjunction with the accompanying drawings:
[0019] as attached Figure 1 to Figure 5 As shown, a three-degree-of-freedom ultrasonic vibration-assisted machining precision positioning platform is an axisymmetric structure of the X-axis and the Y-axis, including a large platform and a small platform 9 integrally formed by wire-cutting of plates, and the center of the large platform is connected in series with the small platform 9 , the bottom of the small platform 9 is connected in series with the bridge amplifying mechanism 5 .
[0020] Four symmetrical differential amplifying mechanisms 4 are symmetrically connected to the outer peripheral side of the bridge-type amplifying mechanism 5 along the X direction and the Y direction through four groups of parallel sheet-shaped flexible hinge...
PUM
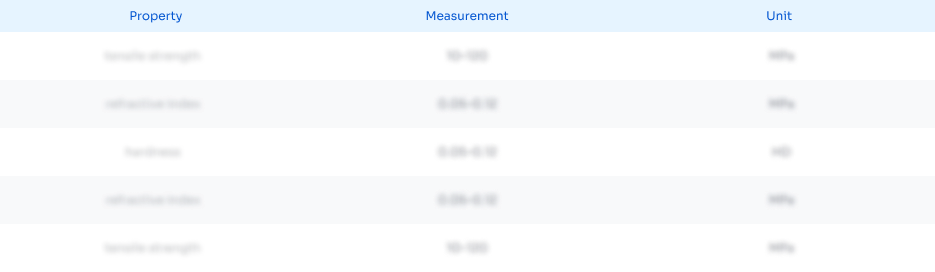
Abstract
Description
Claims
Application Information

- R&D
- Intellectual Property
- Life Sciences
- Materials
- Tech Scout
- Unparalleled Data Quality
- Higher Quality Content
- 60% Fewer Hallucinations
Browse by: Latest US Patents, China's latest patents, Technical Efficacy Thesaurus, Application Domain, Technology Topic, Popular Technical Reports.
© 2025 PatSnap. All rights reserved.Legal|Privacy policy|Modern Slavery Act Transparency Statement|Sitemap|About US| Contact US: help@patsnap.com