Elastic back cavity pipeline vibration reduction and noise reduction device
An elastic and cavity-backed technology, which is applied in the direction of hose connection devices, hoses, pipes, etc., can solve the problems of difficulty in obtaining ideal results, poor vibration damping effect of metal pipes, and insufficient displacement compensation ability, etc., to achieve simple structure, The effect of small elastic modulus and large displacement compensation ability
- Summary
- Abstract
- Description
- Claims
- Application Information
AI Technical Summary
Problems solved by technology
Method used
Image
Examples
Embodiment Construction
[0020] The present invention will be described in detail below with reference to the accompanying drawings.
[0021] refer to figure 1 The outer tube wall 4 is composed of an outer rubber layer 44, a skeleton layer 43 and an inner rubber layer 42. The skeleton layer 43 of the outer tube wall is preferably aramid cord with high strength and high modulus. The inner rubber layer plays a sealing role, the outer rubber layer plays a protective role, and the skeleton layer 43 wraps around the middle flange 41 to prevent pulling out.
[0022] The outer pipe wall and the intermediate flange 41 are vulcanized as one; the two ends of the outer pipe wall 4 are connected and sealed with the inlet end cover 2 and the outlet end cover 7 through bolts 3 and compression flanges 6, and the inlet end cover and the outlet end cover They are respectively connected to the inlet connecting flange 1 and the outlet connecting flange 8, and the inlet connecting flange 1 and the outlet connecting flan...
PUM
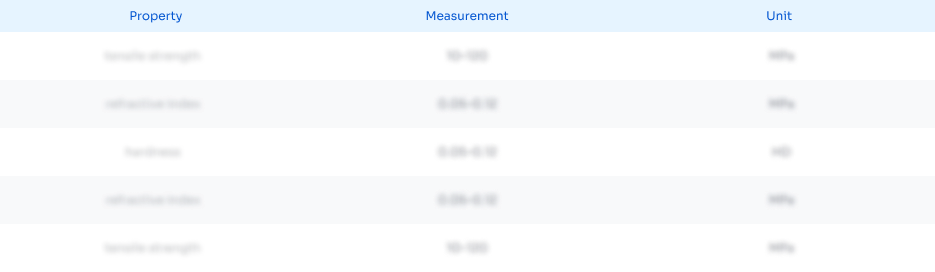
Abstract
Description
Claims
Application Information

- R&D
- Intellectual Property
- Life Sciences
- Materials
- Tech Scout
- Unparalleled Data Quality
- Higher Quality Content
- 60% Fewer Hallucinations
Browse by: Latest US Patents, China's latest patents, Technical Efficacy Thesaurus, Application Domain, Technology Topic, Popular Technical Reports.
© 2025 PatSnap. All rights reserved.Legal|Privacy policy|Modern Slavery Act Transparency Statement|Sitemap|About US| Contact US: help@patsnap.com