Fiber-splitting primary silk spinning assembly for initiatively distributing melts
A technology of active distribution and separation of fibers, which is applied in the direction of spinneret assemblies, textiles and papermaking, etc., can solve problems such as spinning breakage, uneven distribution, and affecting the drawing state, and achieve uniform heat loss and tow crystallization Uniformity and prevention of partial crystallization
- Summary
- Abstract
- Description
- Claims
- Application Information
AI Technical Summary
Problems solved by technology
Method used
Image
Examples
Embodiment l
[0042] As shown in Figure 1-4, a fiber-dividing master filament spinning assembly with active melt distribution includes a housing 1, an upper cover 2, a spacer 3, a distribution cup 4, a melt equalizing plate 5 and a spinneret 6 , the upper cover 2 is located in the upper part of the housing 1, the lower part of the distribution cup 4 is provided with a melt equalizing plate 5 and a spinneret 6 in turn, and the spacer 3 is located between the upper cover 2 and the distribution cup 4; on the spinneret 6 A spinneret hole composed of a spinneret guide hole 13 and a spinneret capillary hole 14 is provided, and the distribution cup 4 is sequentially provided with a deflector 7, a filter sand layer 8, a first filter screen 9, and a second filter screen from top to bottom. Two filter screens 10. A melt equalizing plate 5 is arranged between the distribution cup and the spinneret, and the melt channel in the equalizing plate is a tapered guide hole 11 consistent with the number of sp...
Embodiment 2
[0046] Embodiment 2: The component parameter D used in this example 1 Φ1.35, D 1 / D 2 =2.45.
[0047] Spinning 240D / 12f nylon split fiber mother silk, the raw material is vacuum-packed PA6 sliced screw, the temperature of each zone is 240°C, 269°C, 270°C, 270°C, 270°C, 270°C, the temperature of the box is 275°C, and the side blowing wind speed is 0.7 m / s, wind temperature 20°C, first roll speed 960m / min, temperature 115°C, second roll speed 3800m / min, temperature 145°C, third roll speed 3950m / min, temperature 150°C, winding speed 3850m / min. Spinning is basically normal.
Embodiment 3
[0048] Embodiment 3: The component parameter D used in this example 1 Φ1.65, D 1 / D. 2 =3.
[0049] Spinning 240D / 12f nylon split fiber mother silk, the raw material is vacuum-packed PA6 sliced screw, the temperature of each zone is 240°C, 269°C, 275°C, 275°C, 275°C, 270°C, the temperature of the box is 280°C, and the side blowing wind speed is 0.7 m / s, wind temperature 20°C, first roll speed 960m / min, temperature 115°C, second roll speed 3800m / min, temperature 145°C, third roll speed 3950m / min, temperature 150°C, winding speed 3850m / min. The spinning is basically normal, and the end-break rate is high.
[0050] Below is that each embodiment adopts different component parameters D 1 and D 1 / D 2 Compared with the spinning conditions of the fiber master filament and the evenness and dyeing uniformity data of the fiber:
[0051] Among them, the diameter of the spinneret capillary D 2 for Φ 0.55, the length-to-diameter ratio of the spinneret holes L / D=2.
[0052]
PUM
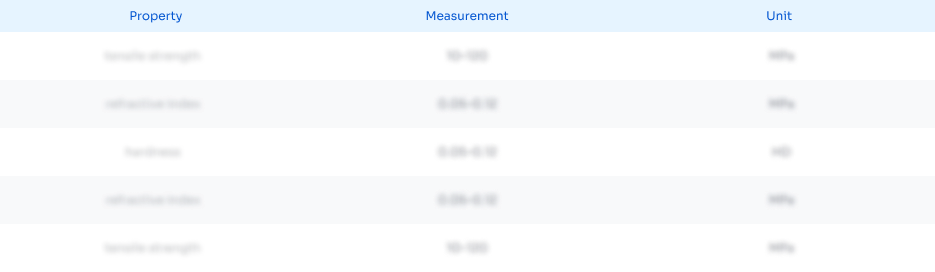
Abstract
Description
Claims
Application Information

- R&D Engineer
- R&D Manager
- IP Professional
- Industry Leading Data Capabilities
- Powerful AI technology
- Patent DNA Extraction
Browse by: Latest US Patents, China's latest patents, Technical Efficacy Thesaurus, Application Domain, Technology Topic, Popular Technical Reports.
© 2024 PatSnap. All rights reserved.Legal|Privacy policy|Modern Slavery Act Transparency Statement|Sitemap|About US| Contact US: help@patsnap.com