An Adaptive Robust Control Method for Electro-hydraulic Servo System Based on Low Frequency Learning
An electro-hydraulic servo system, self-adaptive and robust technology, applied in the direction of self-adaptive control, general control system, control/regulation system, etc., can solve the problems of sliding mode surface flutter, deterioration of control performance, deterioration of system tracking performance, etc. Achieve good tracking performance and avoid high frequency jitter
- Summary
- Abstract
- Description
- Claims
- Application Information
AI Technical Summary
Problems solved by technology
Method used
Image
Examples
Embodiment 1
[0144] In order to assess the performance of the designed controller, the following parameters are taken in the simulation to model the hydraulic system:
[0145] m=30kg, B=8000, A=904.778mm 2 , V=3.98×10 -5 m 3 , P s =10MPa, P r =0
[0146] The desired instruction for a given system is x 1d =0.02sin(t)[1-exp(0.01t 3 )] (m).
[0147] time-varying interference
[0148] White noise (sin(30*pi*t)+50sin(40*pi*t)+50sin(50*pi*t))*0.00001.
[0149] Take the following controller for comparison:
[0150] Adaptive robust controller: take the controller parameter k 1 =300,k 2 =300,k 3 =85,k s =1; parameter initial value Adaptive rate gain Γ 1 =250000, Γ 2 =15000, Γ 3 =0.01, Γ=1×e-6 .
[0151] Adaptive robust low-frequency learning controller: take the controller parameter k 1 =300,k 2 =300,k 3 =85,k s =1; parameter initial value Adaptive rate gain Γ 1 =250000, Γ 2 =15000, Γ 3 =0.01, Γ=1×e -6 ; Correction item gain σ=0.001, Γ f1 =250000, Γ f2 =0.05, Γ f3 ...
PUM
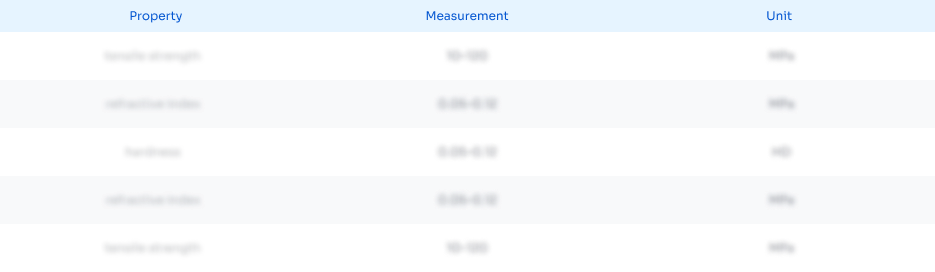
Abstract
Description
Claims
Application Information

- Generate Ideas
- Intellectual Property
- Life Sciences
- Materials
- Tech Scout
- Unparalleled Data Quality
- Higher Quality Content
- 60% Fewer Hallucinations
Browse by: Latest US Patents, China's latest patents, Technical Efficacy Thesaurus, Application Domain, Technology Topic, Popular Technical Reports.
© 2025 PatSnap. All rights reserved.Legal|Privacy policy|Modern Slavery Act Transparency Statement|Sitemap|About US| Contact US: help@patsnap.com