Method for preparing Ga2O3 optoelectronic film by adopting electron beam evaporation technique
A technology of electron beam evaporation and photoelectric thin film, which is applied in the direction of vacuum evaporation plating, ion implantation plating, metal material coating technology, etc., can solve the problems of increasing the difficulty of thin film preparation process, increasing the cost of thin film preparation, and high preparation cost. Achieve good optical transmission performance, abundant raw materials, and low production cost
- Summary
- Abstract
- Description
- Claims
- Application Information
AI Technical Summary
Problems solved by technology
Method used
Image
Examples
Embodiment 1
[0023] 1), with Ga 2 o 3 Powder (purity higher than 99.995%) is used as raw material, the powder is ground and granulated, and then cold-pressed into a cylindrical sample, and then cold isostatic pressed at 100MPa. o Pre-burning in C for 5 hours, and then in a vacuum of 1×10 -1 700 under Pa o C insulation 5h sintering.
[0024] 2) Crush the vacuum-sintered compact into irregular particles of 3-5 mm in size, and place it in a water-cooled crucible in the coating vacuum chamber, and pump the vacuum to 1×10 -3 Pa; while heating the substrate, the heating temperature is 25 o c.
[0025] 3) When the vacuum degree and heating temperature meet the set requirements, open the ventilation valve, and introduce high-purity oxygen (purity 99.999%) into the vacuum chamber, and the oxygen partial pressure is 1.4×10 -2 Pa, and maintain the corresponding vacuum for 5 minutes, and then start coating after stabilization.
[0026] 4) Close the baffle of the evaporation source, turn on the ...
Embodiment 2
[0030] 1) , with Ga 2 o 3 Powder (purity higher than 99.995%) is used as raw material, the powder is ground and granulated, and then cold-pressed into a cylindrical sample, and then cold isostatic pressed at 300MPa. o Pre-burn in C for 1 hour, and then in a vacuum of 1×10 -1 1200 under Pa o C insulation 1h sintering.
[0031] 2) Crush the vacuum sintered compact into irregular particles of 3-5 mm in size, and place them in a water-cooled crucible in the coating vacuum chamber, and pump the vacuum to 1.5×10 -3 Pa; while heating the substrate, the heating temperature is 25 o c.
[0032] 3) When both the vacuum degree and the heating temperature meet the set requirements, open the ventilation valve and introduce high-purity oxygen (purity 99.999%) into the vacuum chamber, and the oxygen partial pressure is 2.6×10 -2 Pa, and maintain the corresponding vacuum for 5 minutes, and then start coating after stabilization.
[0033] 4) Close the baffle of the evaporation source, tu...
Embodiment 3
[0037] 1), with Ga 2 o 3 Powder (purity higher than 99.995%) is used as raw material, the powder is ground and granulated, and then cold-pressed into a cylindrical sample, and then cold isostatic pressed at 150MPa. oPre-burning in C for 3 hours, and then in a vacuum of 5×10 -1 1000 under Pa o C insulation 3h sintering.
[0038] 2) Crush the vacuum-sintered compact into irregular particles of 3-5 mm in size, and place them in a water-cooled crucible in the coating vacuum chamber, and pump the vacuum to 4×10 -3 Pa; while heating the substrate, the heating temperature is 25 o c.
[0039] 3) When the vacuum degree and heating temperature meet the set requirements, open the ventilation valve and feed high-purity oxygen (purity 99.999%) into the vacuum chamber, and the oxygen partial pressure is 1.8×10 -2 Pa, and maintain the corresponding vacuum for 5 minutes, and then start coating after stabilization.
[0040] 4) Close the evaporation source baffle, turn on the electron gu...
PUM
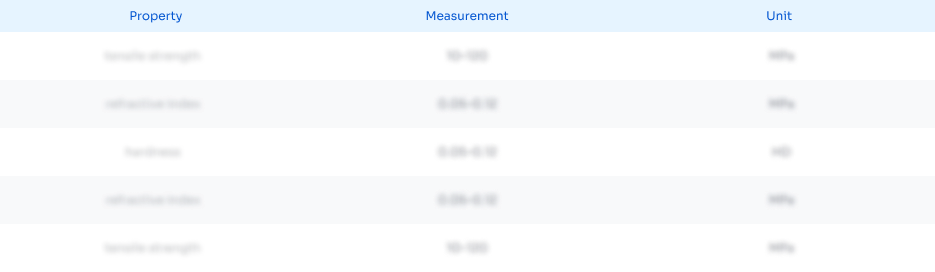
Abstract
Description
Claims
Application Information

- R&D Engineer
- R&D Manager
- IP Professional
- Industry Leading Data Capabilities
- Powerful AI technology
- Patent DNA Extraction
Browse by: Latest US Patents, China's latest patents, Technical Efficacy Thesaurus, Application Domain, Technology Topic, Popular Technical Reports.
© 2024 PatSnap. All rights reserved.Legal|Privacy policy|Modern Slavery Act Transparency Statement|Sitemap|About US| Contact US: help@patsnap.com