Wood composite floor base material and hot pressing device and manufacturing method thereof
A technology of composite floor and hot pressing device, applied in the field of floor manufacturing, can solve the problems of high thermal resistance, fast curing of adhesive, slow board, etc., to achieve the effect of improving mechanical strength, improving response speed and comfort, and speeding up heat transfer
- Summary
- Abstract
- Description
- Claims
- Application Information
AI Technical Summary
Problems solved by technology
Method used
Image
Examples
Embodiment Construction
[0027] The present invention will be further described below in conjunction with the accompanying drawings. The following examples are only used to illustrate the technical solution of the present invention more clearly, but not to limit the protection scope of the present invention.
[0028] The heat transfer of the existing composite flooring with plywood as the base material is vertical to the wood grain direction from bottom to top. Since the thermal conductivity of wood in the vertical direction of wood grain is more than 30% lower than that in the direction along the grain, the thermal conductivity of wood and wood composite floors will be reduced. The resistance is larger, which in turn affects the response speed of indoor space heating, affects the comfort of heating, and affects the utilization efficiency of heat energy. In the present invention, by changing the traditional structure and production process of the base material of the wood composite floor, making full u...
PUM
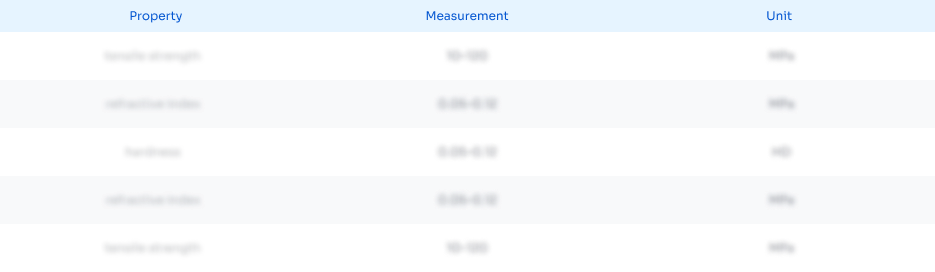
Abstract
Description
Claims
Application Information

- R&D
- Intellectual Property
- Life Sciences
- Materials
- Tech Scout
- Unparalleled Data Quality
- Higher Quality Content
- 60% Fewer Hallucinations
Browse by: Latest US Patents, China's latest patents, Technical Efficacy Thesaurus, Application Domain, Technology Topic, Popular Technical Reports.
© 2025 PatSnap. All rights reserved.Legal|Privacy policy|Modern Slavery Act Transparency Statement|Sitemap|About US| Contact US: help@patsnap.com