Vertical hot sleeving process method for flange end-free long and thin main shaft
A shrink-fit process without flanges, used in metal processing, manufacturing tools, metal processing equipment, etc., can solve the problems of difficulty in assembling components for shrink-fit, over-limited lifting height, etc., shortening the installation cycle, reducing lifting height, heating low cost effect
- Summary
- Abstract
- Description
- Claims
- Application Information
AI Technical Summary
Problems solved by technology
Method used
Image
Examples
Embodiment Construction
[0020] a. Prepare support frame 5, hoisting tool 7, lifting rope, adjusting pad 4, etc. according to the size of the main shaft drawing and the weight of the main shaft, see figure 1 .
[0021] b. Preparation before heat-fitting: spread the high-temperature-resistant and heat-insulating ceramic fiber cloth 9 on the platform, install four lifting lugs on the upper end of the thin-walled part 2, lift the thin-walled part 2 onto the platform, and let the ceramic fiber Place cloth 9 under the thin-walled part 2, and then remove the four lifting lugs, see figure 2 .
[0022] c. Wrap two layers of ceramic fiber cloth 9 on the outer surface of the thin-walled part 2, then wrap the insulated electromagnetic induction wire 8 on the ceramic fiber cloth 9 outside the thin-walled part 2, and wrap it tightly. Thin-walled parts 2 and the upper surface are wrapped with a layer of ceramic fiber cloth 9 for heat preservation, connected to a power supply for heating, see figure 2 .
[002...
PUM
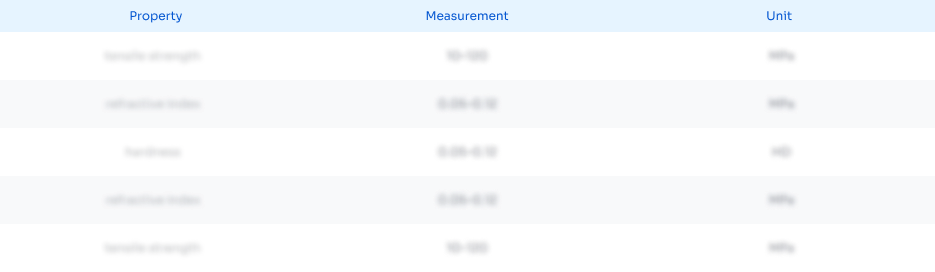
Abstract
Description
Claims
Application Information

- Generate Ideas
- Intellectual Property
- Life Sciences
- Materials
- Tech Scout
- Unparalleled Data Quality
- Higher Quality Content
- 60% Fewer Hallucinations
Browse by: Latest US Patents, China's latest patents, Technical Efficacy Thesaurus, Application Domain, Technology Topic, Popular Technical Reports.
© 2025 PatSnap. All rights reserved.Legal|Privacy policy|Modern Slavery Act Transparency Statement|Sitemap|About US| Contact US: help@patsnap.com