A 3D processing method and 3D processing equipment
A technology of processing equipment and processing methods, applied in the field of 3D printing, can solve problems such as inability to automatically adjust, complex forming processes, and unrecognized systems, and achieve the effects of avoiding forming failures, high-precision processing, and avoiding low forming accuracy.
- Summary
- Abstract
- Description
- Claims
- Application Information
AI Technical Summary
Problems solved by technology
Method used
Image
Examples
Embodiment Construction
[0045] The present invention will be further described below in conjunction with the accompanying drawings and specific embodiments, so that those skilled in the art can better understand the present invention and implement it, but the examples given are not intended to limit the present invention.
[0046] Such as figure 1 Shown, is the 3D processing method in the embodiment of the present invention, and this method comprises the following steps:
[0047] Step S110, the laser additive cladding system performs 3D printing to obtain a 3D printing unit;
[0048] Specifically, the laser additive cladding system performs 3D printing on a multi-axis processing system. The multi-axis processing system is equipped with an X-axis motion mechanism, a Y-axis motion mechanism, and a Z-axis motion mechanism. The two-axis CNC workbench is connected with the X-axis motion mechanism. The two-axis CNC table is used to realize rotation and swing. The Y-axis motion mechanism is connected with ...
PUM
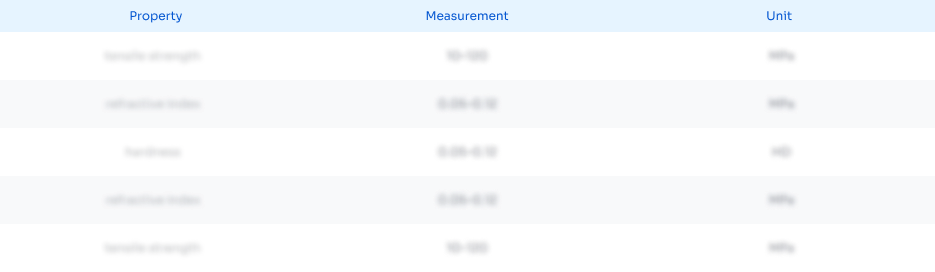
Abstract
Description
Claims
Application Information

- Generate Ideas
- Intellectual Property
- Life Sciences
- Materials
- Tech Scout
- Unparalleled Data Quality
- Higher Quality Content
- 60% Fewer Hallucinations
Browse by: Latest US Patents, China's latest patents, Technical Efficacy Thesaurus, Application Domain, Technology Topic, Popular Technical Reports.
© 2025 PatSnap. All rights reserved.Legal|Privacy policy|Modern Slavery Act Transparency Statement|Sitemap|About US| Contact US: help@patsnap.com