Casting technological method of graphite titanium alloy casting
A casting process and titanium alloy technology, applied in the field of titanium alloy casting, can solve the problems of reducing the quality of casting products, turbulent flow of molten metal, and flow marks on the surface of castings, so as to achieve good equipment adaptability, slow down the drop flow, and facilitate production and operation Effect
- Summary
- Abstract
- Description
- Claims
- Application Information
AI Technical Summary
Problems solved by technology
Method used
Image
Examples
Embodiment 1
[0046] A casting process method for a graphite-type titanium alloy casting, comprising the steps of:
[0047] (1) According to the graphite-type titanium alloy casting (take the optical backplane casting customized by a customer as an example, the casting is a plate-shaped casting with uniform wall thickness, the outline size is: 1030×341×60, the wall thickness is 22mm, figure 1 ), select different casting inclination angles, and build the sprue on the basis of the selected casting inclination angle. Among them, the main sprue of the casting is located at the level of the top surface, which is convenient for the sprue cup to overlap, and the ratio of the cross-sectional area of the casting system Main sprue: horizontal sprue: ingate = 1:2:3, the main sprue is ¢80, and the ingate is set at the thick and large part of the casting, and the casting plan with the corresponding casting inclination angle is obtained; using Huazhu CAE The simulation software performs numerical simul...
Embodiment 2
[0051] A casting process method for a graphite-type titanium alloy casting, comprising the steps of:
[0052] (1) According to the three-dimensional digital model of a graphite-type titanium alloy casting, different casting inclination angles are selected, and the sprue is erected on the basis of the selected casting inclination angle to obtain a casting plan for the corresponding casting inclination angle; use Huazhu CAE simulation software Carry out numerical simulation on the casting plan. When the simulation result shows that the single size of the shrinkage cavity defect in the casting is less than 1.5mm, and the number of defects in each 100mm×100mm×100mm space volume is less than 5, it is determined as the best casting plan, and then the best casting angle is obtained. (45°); Then divide the digital model with the sprue set up on the basis of the best casting angle;
[0053] (2) According to the numerical control programming, program the digital model after the parting ...
Embodiment 3
[0056] A casting process method for a graphite-type titanium alloy casting, comprising the steps of:
[0057] (1) According to the three-dimensional digital model of a graphite-type titanium alloy casting, different casting inclination angles are selected, and the sprue is erected on the basis of the selected casting inclination angle to obtain a casting plan for the corresponding casting inclination angle; use Huazhu CAE simulation software Carry out numerical simulation on the casting plan. When the simulation result shows that the single size of the shrinkage cavity defect in the casting is less than 1.5mm, and the number of defects in each 100mm×100mm×100mm space volume is less than 5, it is determined as the best casting plan, and then the best casting angle is obtained. (35°); Then divide the digital model with the sprue set up on the basis of the best casting angle;
[0058] (2) According to the numerical control programming, program the digital model after the parting ...
PUM
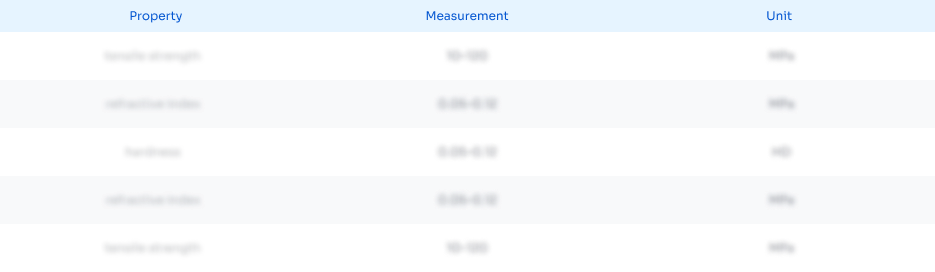
Abstract
Description
Claims
Application Information

- R&D
- Intellectual Property
- Life Sciences
- Materials
- Tech Scout
- Unparalleled Data Quality
- Higher Quality Content
- 60% Fewer Hallucinations
Browse by: Latest US Patents, China's latest patents, Technical Efficacy Thesaurus, Application Domain, Technology Topic, Popular Technical Reports.
© 2025 PatSnap. All rights reserved.Legal|Privacy policy|Modern Slavery Act Transparency Statement|Sitemap|About US| Contact US: help@patsnap.com