Method of forming components from sheet material
A sheet and component technology, applied in the improvement field of forming components from alloy sheet metal, can solve problems such as different chemical properties of precipitates
- Summary
- Abstract
- Description
- Claims
- Application Information
AI Technical Summary
Problems solved by technology
Method used
Image
Examples
Embodiment Construction
[0053] figure 1 A conventional pressing process for forming a part from a sheet metal blank is shown. The first stage involves heating the sheet stock to at least its solvus temperature, for example in an oven or heating station. The solvus temperature is an intrinsic property of the particular metal or alloy formed. The sheet blank is then transferred to a press, such as a hydraulic press. The press seal is activated and the companion tool presses the sheet and forms it into its final shape in one step. The part is quenched under cold tool and load and oven hardened to achieve the desired level of hardening. The final product can then be cooled and used. While this arrangement is capable of forming complex shapes, the rapid attainment of the complete final shape of complex shapes and subsequent quenching steps between cold tools may result in less than desired dislocation recovery and failure to achieve desired material properties.
[0054] The present invention aims to...
PUM
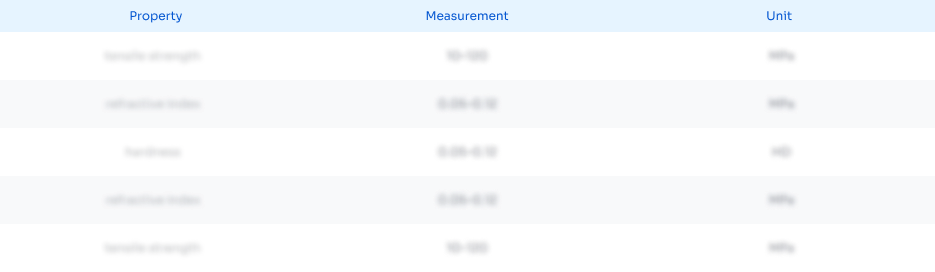
Abstract
Description
Claims
Application Information

- R&D
- Intellectual Property
- Life Sciences
- Materials
- Tech Scout
- Unparalleled Data Quality
- Higher Quality Content
- 60% Fewer Hallucinations
Browse by: Latest US Patents, China's latest patents, Technical Efficacy Thesaurus, Application Domain, Technology Topic, Popular Technical Reports.
© 2025 PatSnap. All rights reserved.Legal|Privacy policy|Modern Slavery Act Transparency Statement|Sitemap|About US| Contact US: help@patsnap.com