Shock-resistant assembly self-locking type rolling half grouting sleeve
A semi-grouting sleeve, self-locking technology, applied in the direction of structural elements, building components, building reinforcements, etc., can solve the problems of difficult processing, bulky sleeve shape, poor deformation resistance, etc., to control the quality of threaded connections, The effect of easy screw connection quality and reduction of rolling deformation
- Summary
- Abstract
- Description
- Claims
- Application Information
AI Technical Summary
Problems solved by technology
Method used
Image
Examples
Embodiment 1
[0067] Such as figure 1 , figure 2 , image 3 As shown, an anti-seismic assembled self-locking rolling semi-grouting sleeve, including a sleeve 5, a steel pipe transition section 7, and a self-locking steel skeleton 4;
[0068] The sleeve 5 is made of seamless steel pipe, and the sleeve 5 includes a non-grouting connection section 51 and a grouting connection section 52; the grouting connection section 52 is processed by rolling to form grooves 523 on the outer wall and convex ribs 522 on the inner wall. Both ends of the grouting connection section 52 are provided with a grouting hole 521 and a vent hole 511 respectively, and the vent hole 511 is close to the non-grouting connection section 51. In order to ensure sufficient grouting, the present embodiment can also design the diameter of the vent hole 511 The diameter is smaller than the diameter of the grouting hole 521, so that the grouting amount is greater than the grouting amount, thereby ensuring that the grouting in ...
Embodiment 3
[0086] A processing method for fabricated concrete components, comprising the following steps:
[0087] Step 1. Binding of reinforced skeleton of prefabricated concrete members
[0088] One end of the first steel bar 11 to be connected is bound and fixed with other steel bars to form a reinforced skeleton of the fabricated concrete member. The other end of the first steel bar to be connected is inserted into the rolling section 71 of the steel pipe transition section 7, and the steel pipe transition section 7 is realized by rolling machinery. The connection with the first steel bar 11 to be connected, so that the self-locking semi-grouting sleeve 5 is pre-installed in the reinforced skeleton of the prefabricated concrete member;
[0089] Step 2. Pouring of prefabricated concrete elements
[0090] Connect the plastic pipe 8 to the grouting hole 521 and the vent hole 511 on the side wall of the sleeve 5 and lead it out of the component formwork, then the concrete placing machine ...
Embodiment 4
[0094] Such as Figure 8 , Figure 9 As shown, the on-site installation method of prefabricated concrete components:
[0095] Step 1. Installation preparation: Before hoisting the prefabricated concrete components, prepare the necessary tools and materials for grouting, clean the foundation surface of the connection part, check the horizontal position and reserved length of the second steel bar 12 to be connected, and check the hoisting equipment, and according to The elevation control value made by the on-site setting-out, place the adjustable block 20 on the base surface of the connection part to adjust the height when the subsequent prefabricated concrete member is installed;
[0096] Step 2. Hoisting: Use a mirror to observe and insert the lower second steel bars 12 to be connected one by one into the grouting sleeve 5 of the upper prefabricated concrete member, and then use the tower crane to slowly place the prefabricated concrete member on the adjustable pad 20;
[00...
PUM
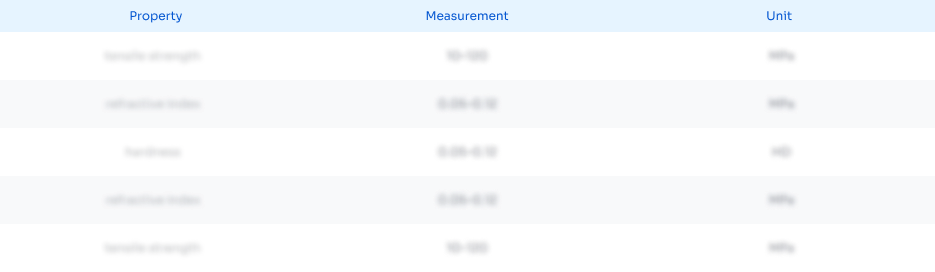
Abstract
Description
Claims
Application Information

- R&D
- Intellectual Property
- Life Sciences
- Materials
- Tech Scout
- Unparalleled Data Quality
- Higher Quality Content
- 60% Fewer Hallucinations
Browse by: Latest US Patents, China's latest patents, Technical Efficacy Thesaurus, Application Domain, Technology Topic, Popular Technical Reports.
© 2025 PatSnap. All rights reserved.Legal|Privacy policy|Modern Slavery Act Transparency Statement|Sitemap|About US| Contact US: help@patsnap.com