Production process of wool fabric
A production process and wool technology, applied in the processing of textile materials, fabric surface trimming, liquid/gas/steam textile processing, etc., can solve the problems of large shrinkage and deformation, affecting the service life, etc., and achieve suitable temperature and anti-felt shrinkage. good effect
- Summary
- Abstract
- Description
- Claims
- Application Information
AI Technical Summary
Problems solved by technology
Method used
Examples
Embodiment 1
[0016] A production process for wool fabrics, including dyeing, spinning and weaving steps, washing raw wool and then dyeing, adding leveling agent, auxiliary agent and antistatic agent in the dyeing process, the auxiliary agent is acetic acid, after the weaving step also includes Finishing process, the finishing steps include soaking, shrinking, drying, shearing and ball rolling,
[0017] Soak the wool fabric in water at 38°C for 3 minutes;
[0018] Put the softening agent accounting for 3% of the wool fabric weight in the shrinking machine, put the wool fabric, soak for 20 minutes, then open the shrinking machine for shrinking, the shrinking time is 10 minutes, and the rotating speed is 20 rpm;
[0019] Under the condition of 120°C, the wool fabric after milling is tentered at a speed of 3m / min;
[0020] Trim the dried wool fabric and trim off 3 mm fluff;
[0021] Preheat the ball rolling machine to 80°C, feed the wool fabric, heat up to 130°C, keep warm for 3 minutes, hum...
Embodiment 2
[0023] A production process for wool fabrics, including dyeing, spinning and weaving steps, washing raw wool and then dyeing, adding leveling agent, auxiliary agent and antistatic agent in the dyeing process, the auxiliary agent is acetic acid, after the weaving step also includes Finishing process, the finishing steps include soaking, shrinking, drying, shearing and ball rolling,
[0024] Soak the woolen fabric in water at 39°C for 4 minutes;
[0025] Put into the shrinking machine the softener that accounts for 4% of the weight of the wool fabric, put the wool fabric into it, soak for 25 minutes, then open the shrinking machine for shrinking, the shrinking time is 11 minutes, and the rotating speed is 25 rpm;
[0026] Under the condition of 140°C, the wool fabric after milling is tentered at a speed of 4m / min;
[0027] Trim the dried wool fabric to remove 4mm fluff;
[0028] Preheat the ball rolling machine to 82°C, feed the wool fabric, raise the temperature to 130°C, kee...
Embodiment 3
[0030] A production process for wool fabrics, including dyeing, spinning and weaving steps, the raw material wool is washed and then dyed, adding leveling agent, auxiliary agent and antistatic agent in the dyeing process, the auxiliary agent is acetic acid, after the weaving step It also includes the finishing process, which includes soaking, shrinking, drying, shearing and ball rolling,
[0031] Soak the woolen fabric in water at 40°C for 5 minutes;
[0032] Put into the shrinking machine the softening agent that accounts for 5% of the wool fabric weight, put into the wool fabric, soak for 30 minutes, then open the shrinking machine and carry out shrinking, the shrinking time is 12 minutes, and the rotating speed is 30 rpm;
[0033] Under the condition of 160°C, the wool fabric after milling is tentered at a speed of 5m / min;
[0034] Trim the dried wool fabric to remove 5mm fluff;
[0035] Preheat the ball rolling machine to 85°C, feed the wool fabric, raise the temperature...
PUM
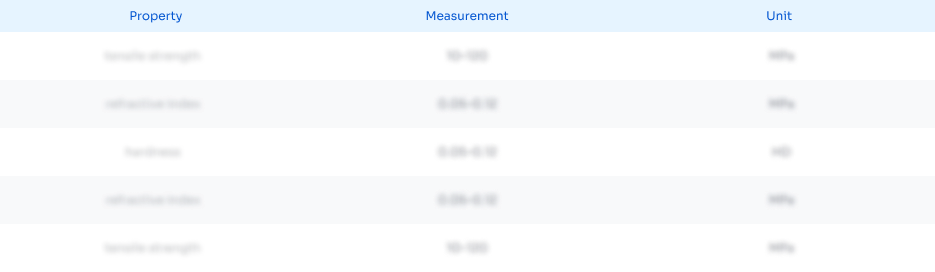
Abstract
Description
Claims
Application Information

- R&D
- Intellectual Property
- Life Sciences
- Materials
- Tech Scout
- Unparalleled Data Quality
- Higher Quality Content
- 60% Fewer Hallucinations
Browse by: Latest US Patents, China's latest patents, Technical Efficacy Thesaurus, Application Domain, Technology Topic, Popular Technical Reports.
© 2025 PatSnap. All rights reserved.Legal|Privacy policy|Modern Slavery Act Transparency Statement|Sitemap|About US| Contact US: help@patsnap.com