Method of preparing peroxide vulcanized fluororubber through nano emulsion polymerization
A technology for vulcanizing fluororubber and nanoemulsion, which is applied in the field of nanoemulsion polymerization to prepare peroxide vulcanized fluororubber, can solve the problems of reduced equipment utilization rate, low solid content, affecting production efficiency, etc., so as to improve production efficiency and improve emulsion concentration. , the effect of excellent mechanical properties and processability
- Summary
- Abstract
- Description
- Claims
- Application Information
AI Technical Summary
Problems solved by technology
Method used
Examples
Embodiment 1
[0022] Embodiment 1: in the container of 10L, add the deionized water of 4kg, 3.8kg structural formula is CF3O(CF(CF3)CF2O)COONHThe fluoroether carboxylate, 1.6kg structural formula is CF3O(CF(CF3)CF2O)10( CF2CF2O)4CF3 The fluoroether oil is stirred evenly under normal temperature and pressure, and the aqueous solution of the microemulsion surfactant with a concentration of 57.4% is obtained.
Embodiment 2
[0023] Example 2: Taking a 10L polymerization kettle as an example, add 6kg of ion-free water, 0.3kg of the microemulsion surfactant prepared in Example 1 and the vulcanization point monomer 4-bromo-3,3,4,4 into the reaction kettle -Tetrafluoro-1-butene 12g, 1,6-diiododecafluorohexane 7g; After nitrogen replacement and vacuum treatment, after the oxygen content in the kettle is ≤20ppm; the mass ratio of adding to the kettle is 25:38 : 37 mixed monomers of tetrafluoroethylene, vinylidene fluoride, and hexafluoropropylene, until the pressure of the kettle is 1.8 Mpa; stir, heat up to 80°C, add 140g of ammonium persulfate initiator with a concentration of 5% to start the reaction, during the reaction Continuously add the monomer mixture to keep the pressure at 1.8Mpa; stop the reaction after a certain amount of reaction, and recover the unreacted mixed monomer after cooling; the latex obtained by polymerization is coagulated, washed, dried and dehydrated, and then obtained by the ...
Embodiment 3
[0024] Example 3: Taking a 20L polymerization kettle as an example, add 12kg of deionized water, 0.6kg of the microemulsion surfactant prepared in Example 1 and the vulcanization point monomer 4-bromo-3,3,4,4 in the reaction kettle -Tetrafluoro-1-butene 24g, 1,6-diiododecafluorohexane 14g; After nitrogen replacement and vacuum treatment, after the oxygen content in the kettle is ≤20ppm; the mass ratio of adding to the kettle is 25:38 : 37 mixed monomers of tetrafluoroethylene, vinylidene fluoride, and hexafluoropropylene, until the pressure of the kettle is 2.0Mpa; stir, heat up to 82°C, add 300g of ammonium persulfate initiator with a concentration of 5% to start the reaction, during the reaction Continuously add the monomer mixture to keep the pressure at 2.0Mpa; stop the reaction after a certain amount of reaction, and recover the unreacted mixed monomer after cooling; the latex obtained by polymerization is coagulated, washed, dried and dehydrated, and then obtained by the ...
PUM
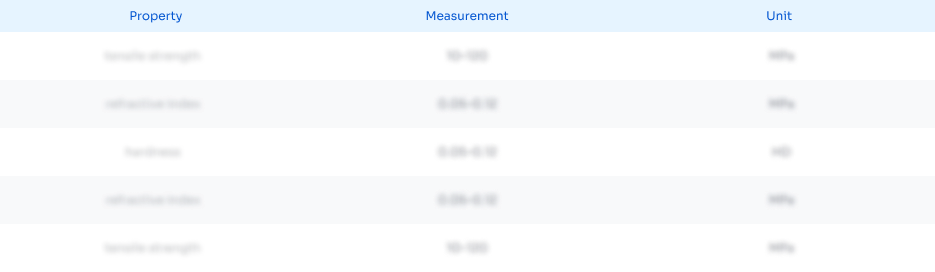
Abstract
Description
Claims
Application Information

- R&D
- Intellectual Property
- Life Sciences
- Materials
- Tech Scout
- Unparalleled Data Quality
- Higher Quality Content
- 60% Fewer Hallucinations
Browse by: Latest US Patents, China's latest patents, Technical Efficacy Thesaurus, Application Domain, Technology Topic, Popular Technical Reports.
© 2025 PatSnap. All rights reserved.Legal|Privacy policy|Modern Slavery Act Transparency Statement|Sitemap|About US| Contact US: help@patsnap.com