Non-fire-worker-driven two-stage compressing releasing mechanism
A release mechanism, non-pyrotechnic technology, applied in the direction of motor vehicles, space navigation equipment, space navigation aircraft, etc., can solve the problems of mismatching driving force, failure of normal release of mechanism, performance degradation of SMA wire, etc.
- Summary
- Abstract
- Description
- Claims
- Application Information
AI Technical Summary
Problems solved by technology
Method used
Image
Examples
Embodiment Construction
[0040] The drive mode of the slider in the present invention is non-pyrotechnic drive, and different drive elements such as electromagnetic drive, paraffin drive, SMA drive, etc. can be selected according to the application occasion. Two specific implementations of the present invention will be described below in conjunction with the accompanying drawings.
[0041] figure 1 An embodiment of the present invention is given, specifically, an electromagnetically driven two-stage compression release mechanism is used, and the electromagnet 18 is selected as a non-pyrotechnic driving element to drive the slider. Such as figure 1 As shown, the separation cap 1 is installed on the upper cage 2, and is limited by the upper ball 3, and the position of the upper ball 3 is jointly determined by the separation cap 1, the upper cage 2 and the release pin 10; The bottom of the upper ball 3 is set on the upper cage 2, and can slide up and down in the rectangular track on the upper cage 2; t...
PUM
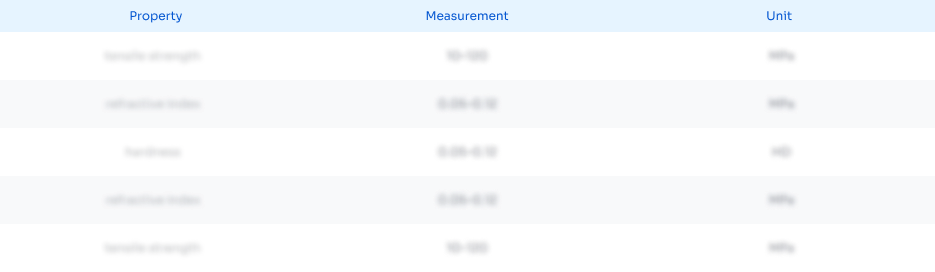
Abstract
Description
Claims
Application Information

- R&D
- Intellectual Property
- Life Sciences
- Materials
- Tech Scout
- Unparalleled Data Quality
- Higher Quality Content
- 60% Fewer Hallucinations
Browse by: Latest US Patents, China's latest patents, Technical Efficacy Thesaurus, Application Domain, Technology Topic, Popular Technical Reports.
© 2025 PatSnap. All rights reserved.Legal|Privacy policy|Modern Slavery Act Transparency Statement|Sitemap|About US| Contact US: help@patsnap.com