Positioning and checking tool for side vertical control over optical prisms and processing method
A positioning tooling and side positioning technology, which is applied in the direction of manufacturing tools, optical surface grinders, metal processing equipment, etc., can solve the problem that the positioning accuracy of side sagging is difficult to achieve, and achieve simple and fast positioning, avoid loosening or falling, and increase bonding intensity effect
- Summary
- Abstract
- Description
- Claims
- Application Information
AI Technical Summary
Problems solved by technology
Method used
Image
Examples
Embodiment 1
[0048] Such as image 3 As shown, a positioning tool for optical prism side sag control in this embodiment is specially designed for grinding the bevels at both ends of a square prism. figure 1 The semi-finished square prism shown is ground into figure 2 Finished product shown. The square prism requires that the angle between the inclined surfaces at both ends and the upper and lower bottom surfaces is 45°, and the perpendicularity accuracy with the front and rear sides, that is, the side sag accuracy is within 20". The positioning tool structure will be described below.
[0049] The positioning tool of this embodiment includes a base plate 1 , a positioning prism 2 , an end face positioning block 3 , a side positioning block 4 , a connecting block 5 and a supporting block 6 . Wherein, the positioning prism 2, the end face positioning block 3 and the supporting block 6 are placed on the substrate 1; the positioning prism 2 and the side positioning block 4 are all isosceles ...
Embodiment 2
[0054] Such as Figure 4 As shown, a calibration tool for side sag control of an optical prism in this embodiment is specially designed for the positioning and installation of the positioning tool for side sag control of an optical prism in Embodiment 1. It mainly comprises a reference triangular prism 7 and a reference square prism 8; wherein, the reference triangular prism 7 is an isosceles right-angled prism, the reference square prism 8 is fixed on the slope of the reference triangular prism 7, and the reference square prism 8 is a regular hexagon. Reference triangular prism 7 cooperates with the V-shaped positioning groove that two positioning triangular prisms 2 form, wherein two adjacent sides of reference square prism 8 are used as detection surfaces, cooperate with the end positioning surface of end face positioning block 3 and the side positioning block 4 respectively. Side locating face fit.
[0055] The reference triangular prism 7 and the reference square prism 8...
Embodiment 3
[0059] A kind of processing method of side sagging control of optical prism in this embodiment is used to figure 1 The semi-finished square prism shown is processed into figure 2 For the finished square prism shown, the bevels at both ends are ground and processed to ensure that the side sag accuracy of the bevel and the front and rear sides of the square prism is within 20″.
[0060] The operation steps of the processing method of optical prism side sag control are as follows:
[0061] 1. Assembly of positioning tooling
[0062] Adopt the positioning tooling of the optical prism side droop control of the optical prism side droop control of the optical prism side droop control in the assembly embodiment 1 of embodiment 2; Figure 5 As shown, the specific assembly steps are:
[0063] ①Take a positioning prism 2 and press it on the upper surface of the substrate 1 to generate interference fringes, and glue it together with optical glue; put the V-shaped bottom side of the re...
PUM
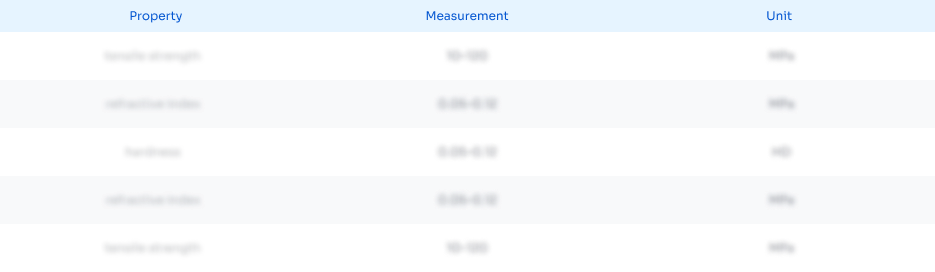
Abstract
Description
Claims
Application Information

- R&D Engineer
- R&D Manager
- IP Professional
- Industry Leading Data Capabilities
- Powerful AI technology
- Patent DNA Extraction
Browse by: Latest US Patents, China's latest patents, Technical Efficacy Thesaurus, Application Domain, Technology Topic, Popular Technical Reports.
© 2024 PatSnap. All rights reserved.Legal|Privacy policy|Modern Slavery Act Transparency Statement|Sitemap|About US| Contact US: help@patsnap.com