Novel raw material vertical milling and preparing system
A raw material vertical mill and preparation system technology, applied in grain processing, etc., can solve the problems of difficult confirmation of grinding efficiency, lack of adaptability, low manufacturing cost, etc., to reduce the burden of grinding, increase compactness, and material layer stable effect
- Summary
- Abstract
- Description
- Claims
- Application Information
AI Technical Summary
Problems solved by technology
Method used
Image
Examples
Embodiment 1
[0026] refer to figure 1 , the preferred embodiment 1 of the present invention provides a novel raw material vertical mill preparation system, comprising a feeding belt 1, an air lock feeding device 2, a vertical mill 3, a cyclone 10, a circulating fan 11, and a circulating air duct 12 connected in sequence , also includes a spiral reamer 4, a hoist 5, a roller press feed chamber 6, a roller press 7, and a roller press discharge hopper hoist 9 connected in sequence; wherein, the spiral reamer 4 is connected with the vertical mill The coarse powder feeding pipe of the vertical mill separator 3-1 is connected to the vertical mill separator coarse powder out of the vertical mill 3, and the vertical mill is separated by the hoist 5 and the roller press feeding small chamber 6. The coarse powder of the pulverizer is sent to the roller press 7 for extrusion and grinding; the discharge port of the hopper elevator 9 of the roller press is connected with the feeding belt 1, and the pow...
Embodiment 2
[0029] refer to figure 2 , the preferred embodiment 2 of the present invention provides a novel raw material vertical mill preparation system, comprising a feeding belt 1, an air lock feeding device 2, a vertical mill 3, a cyclone 10, a circulating fan 11, and a circulating air duct 12 connected in sequence , also includes a spiral reamer 4, a hoist 5, a roller press feed chamber 6, a roller press 7, and a roller press discharge hopper hoist 9 connected in sequence; wherein, the spiral reamer 4 is connected with the vertical mill The coarse powder feeding pipe of the vertical mill separator 3-1 is connected to the vertical mill separator coarse powder out of the vertical mill 3, and the vertical mill is separated by the hoist 5 and the roller press feeding small chamber 6. The coarse powder of the pulverizer is sent to the roller press 7 for extrusion and grinding; the discharge port of the hopper elevator 9 of the roller press is connected with the feeding belt 1, and the po...
Embodiment 3
[0033] refer to image 3, the preferred embodiment 3 of the present invention provides a novel raw material vertical mill preparation system, comprising a feeding belt 1, an air lock feeding device 2, a vertical mill 3, a cyclone 10, a circulating fan 11, and a circulating air duct 12 connected in sequence , also includes a spiral reamer 4, a hoist 5, a roller press feed chamber 6, a roller press 7, and a roller press discharge hopper hoist 9 connected in sequence; wherein, the spiral reamer 4 is connected with the vertical mill The coarse powder feeding pipe of the vertical mill separator 3-1 is connected to the vertical mill separator coarse powder out of the vertical mill 3, and the vertical mill is separated by the hoist 5 and the roller press feeding small chamber 6. The coarse powder of the pulverizer is sent to the roller press 7 for extrusion and grinding; the discharge port of the hopper elevator 9 of the roller press is connected with the feeding belt 1, and the powd...
PUM
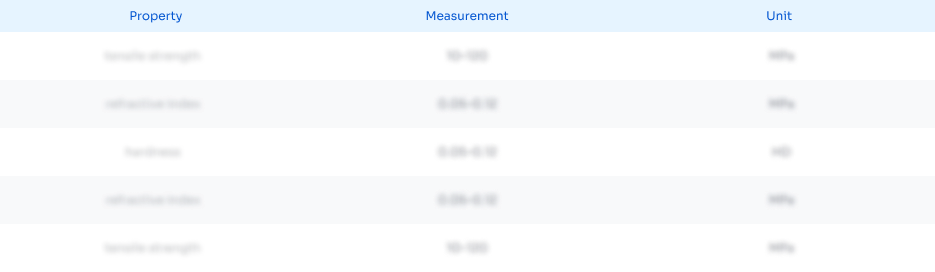
Abstract
Description
Claims
Application Information

- R&D Engineer
- R&D Manager
- IP Professional
- Industry Leading Data Capabilities
- Powerful AI technology
- Patent DNA Extraction
Browse by: Latest US Patents, China's latest patents, Technical Efficacy Thesaurus, Application Domain, Technology Topic, Popular Technical Reports.
© 2024 PatSnap. All rights reserved.Legal|Privacy policy|Modern Slavery Act Transparency Statement|Sitemap|About US| Contact US: help@patsnap.com