Method and system for evaluating raw material melting evenness in basalt tank furnace
A homogeneity and basalt technology, applied in design optimization/simulation, special data processing applications, instruments, etc., can solve problems such as poor melting uniformity, small production scale, and low efficiency, and achieve low cost, simple method, and easy promotion and use Effect
- Summary
- Abstract
- Description
- Claims
- Application Information
AI Technical Summary
Problems solved by technology
Method used
Image
Examples
Embodiment 1
[0053]For a basalt pool kiln, the length, width, and height are 5m, 1m, and 0.4m, respectively, and the average residence time of the melt is 12h. figure 2 As shown, the evaluation process on the homogeneity of raw material melting includes the following steps in sequence:
[0054] 1) Obtain the temperature field and velocity field distribution of the melt in the basalt kiln, set the grid scale to 40mm, divide the kiln area into 350,000 grids, and number each grid;
[0055] 2) Discretize the melt information in the flow area of the above-mentioned tank kiln, including the three continuous data of temperature, viscosity (which is a function of temperature), and flow velocity, so as to define the melt flow information of each grid unit ;
[0056] 3) At the initial moment, put 16,000 massless tracer particles at the entrance of the melt flow area of the tank kiln, and number each particle;
[0057] 4) The time step Δt is defined as 60s, and the melt flow velocity of the gr...
Embodiment 2
[0064] On the basis of Example 1, 10 electrodes were added to the tank kiln, and the final melting uniformity index MIU=0.6235 was obtained by the above steps.
[0065] From the comparison of the melting uniformity index calculated by Example 1 and Example 2, the melting uniformity of Example 2 is obviously better than that of Example 1, and in actual production, it is the addition of electrodes that ensures The temperature uniformity of the melt in the upper and lower layers of the pool kiln prevents the melt from cooling and crystallizing at the bottom of the kiln.
[0066] Therefore, the method established by the present invention can quantitatively evaluate the uniformity of raw material melting in the basalt pool kiln, which has good engineering application value for the structural design of the pool kiln and the optimization of the operation process.
PUM
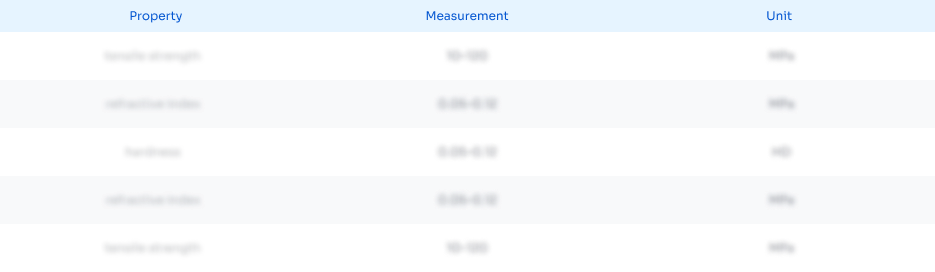
Abstract
Description
Claims
Application Information

- Generate Ideas
- Intellectual Property
- Life Sciences
- Materials
- Tech Scout
- Unparalleled Data Quality
- Higher Quality Content
- 60% Fewer Hallucinations
Browse by: Latest US Patents, China's latest patents, Technical Efficacy Thesaurus, Application Domain, Technology Topic, Popular Technical Reports.
© 2025 PatSnap. All rights reserved.Legal|Privacy policy|Modern Slavery Act Transparency Statement|Sitemap|About US| Contact US: help@patsnap.com