Thermal barrier coating working condition simulation and real-time monitoring device
A technology of working condition simulation and real-time monitoring, applied in the field of aero-engines, can solve problems such as failure to meet actual needs, low integration, harsh multi-field coupling service environment of aero-engines, etc.
- Summary
- Abstract
- Description
- Claims
- Application Information
AI Technical Summary
Problems solved by technology
Method used
Image
Examples
Embodiment Construction
[0023] In order to make the object, technical solution and advantages of the present invention clearer, the present invention will be further described in detail below in combination with specific embodiments and with reference to the accompanying drawings. It should be understood that these descriptions are exemplary only, and are not intended to limit the scope of the present invention. Also, in the following description, descriptions of well-known structures and techniques are omitted to avoid unnecessarily obscuring the concept of the present invention.
[0024] refer to figure 1, The thermal barrier coating working condition simulation and real-time monitoring device described in this embodiment includes: a box body 10000, a working condition simulation component 20000, a sample clamping component 50000, a monitoring component 60000 and a system control component 70000; a working condition simulation component 20000 Used to simulate the working environment of the sample ...
PUM
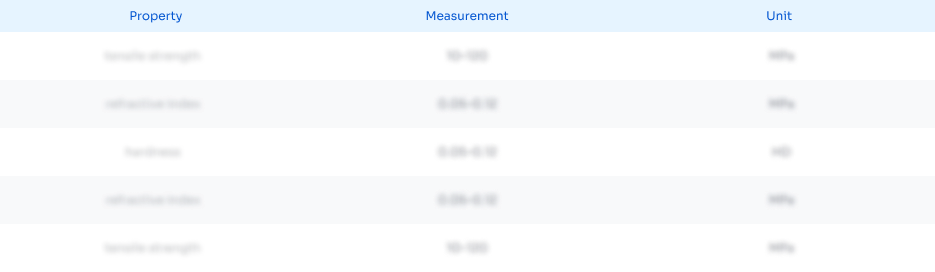
Abstract
Description
Claims
Application Information

- R&D Engineer
- R&D Manager
- IP Professional
- Industry Leading Data Capabilities
- Powerful AI technology
- Patent DNA Extraction
Browse by: Latest US Patents, China's latest patents, Technical Efficacy Thesaurus, Application Domain, Technology Topic, Popular Technical Reports.
© 2024 PatSnap. All rights reserved.Legal|Privacy policy|Modern Slavery Act Transparency Statement|Sitemap|About US| Contact US: help@patsnap.com