A six-degree-of-freedom ultra-low frequency vibration isolation device and its control system based on a zero-stiffness system
A zero-stiffness, degree-of-freedom technology, applied in the field of six-degree-of-freedom vibration isolation devices and their control systems, can solve problems such as few studies, and achieve the effect of low cost and simple structure
- Summary
- Abstract
- Description
- Claims
- Application Information
AI Technical Summary
Problems solved by technology
Method used
Image
Examples
specific Embodiment approach 1
[0059] Specific implementation mode one: as figure 1 , figure 2 and Figure 7 Shown, in conjunction with accompanying drawing, the scheme of the present invention is described in detail:
[0060] A six-degree-of-freedom ultra-low frequency vibration isolation device based on a zero-stiffness system. The zero-stiffness system refers to a system that does not have the ability to resist elastic deformation, has continuous balance, constant potential energy, and neutral stability. Its dynamic equation can be expressed as for
[0061]
[0062] Where X is the displacement vector of the system, ε is the acceleration vector; the zero-stiffness system has the characteristics of zero natural frequency, and can realize low-frequency, ultra-low-frequency, and even low-frequency full-frequency vibration immune vibration isolation performance;
[0063] The configuration of the six-degree-of-freedom ultra-low-frequency vibration isolation device (six-degree-of-freedom ultra-low-frequ...
specific Embodiment approach 2
[0097] Specific implementation mode two: as figure 1 and image 3 As shown, other specific implementations of a single vibration isolation module are given:
[0098] The connecting assembly between the springs includes two rollers 1, two guide rails 3, and an intermediate wheel 4, and the horizontal spring includes two horizontal compression springs 2;
[0099] The two guide rails 3 are respectively fixed in the middle of the inner wall of the cylindrical housing 10, and the two are symmetrically distributed. There is a horizontal compression spring 2, the middle wheel 4 is located between the two rollers 1, the upper part of the middle wheel 4 is fixedly connected with the lower end of the upper connecting rod 11, the lower part of the middle wheel 4 is fixedly connected with the upper end of the vertical spring 5, and the middle wheel 4 under the action of the roller 1 located on both sides of it along the q i direction movement; the lower end of the vertical spring 5 is...
specific Embodiment approach 3
[0106] Specific implementation mode three: as figure 1 and Figure 4 As shown, other specific implementations of a single vibration isolation module are given:
[0107] The connecting assembly between the springs includes two sliders 1, two guide rails 3, and two connecting rods 4, and the horizontal spring includes two horizontal compression springs 2;
[0108] Two guide rails 3 are respectively fixed in the middle of the inner wall of the cylindrical housing 10, and the two are symmetrically distributed. Each slider 1 is placed in the corresponding guide rail 3, and each slider 1 and the inner wall of the corresponding cylindrical housing 10 There is a horizontal compression spring 2 between them, one end of each connecting rod 4 is hinged to the center of the corresponding slider 1, the other ends of the two connecting rods 4 are hinged, and the two connecting rods 4 are located between the two sliders 1,
[0109] The hinged parts of the two connecting rods 4 are connect...
PUM
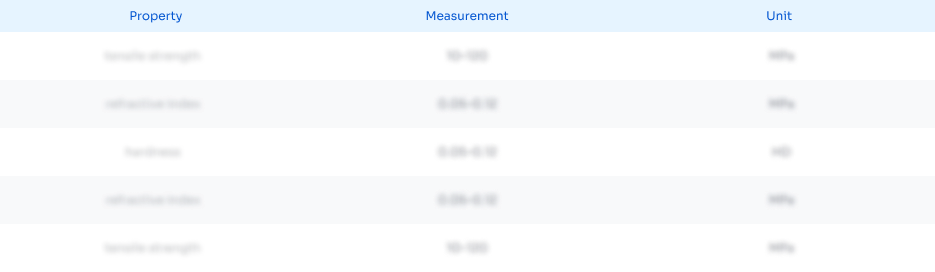
Abstract
Description
Claims
Application Information

- Generate Ideas
- Intellectual Property
- Life Sciences
- Materials
- Tech Scout
- Unparalleled Data Quality
- Higher Quality Content
- 60% Fewer Hallucinations
Browse by: Latest US Patents, China's latest patents, Technical Efficacy Thesaurus, Application Domain, Technology Topic, Popular Technical Reports.
© 2025 PatSnap. All rights reserved.Legal|Privacy policy|Modern Slavery Act Transparency Statement|Sitemap|About US| Contact US: help@patsnap.com