Method for producing polyaluminium chloride by-product of producing diethyl methylphosphonite
A technology of diethyl methyl phosphite and polyaluminum chloride, applied in the direction of aluminum chloride, aluminum halide, alkali metal chloride, etc., can solve pollution, high equipment requirements, increase the consumption of hydrochloric acid and water treatment costs, etc. problem, to achieve the effect of simple process and low cost
- Summary
- Abstract
- Description
- Claims
- Application Information
AI Technical Summary
Problems solved by technology
Method used
Image
Examples
Embodiment 1
[0042] The present invention includes the following steps:
[0043] (1). 7 parts of sodium tetrachloroaluminate, a by-product rich in sodium tetrachloroaluminate during the production of diethyl methylphosphonite, is slowly poured into the dissolving kettle for dissolution, and then solid-liquid separation is carried out. Take out the sodium chloride crystals and collect the solution;
[0044] (2) Add the collected solution to the reactor, then add 0.2 part of ferric chloride and 1 part of hydrochloric acid, and stir and mix for 15 minutes;
[0045] (3) Control the temperature of the reactor to be above 85°C; add 0.1 part of aluminum hydroxide and 2 parts of calcium metaaluminate in order for polymerization reaction;
[0046] (4), control the temperature to 100℃, keep the temperature for 75min;
[0047] (5) Separate after cooling, and the filtrate is the product of the invention.
[0048] Before the polymerization reaction, 0.01 part of industrial white oil was added as a defoaming agen...
Embodiment 2
[0052] The present invention includes the following steps:
[0053] (1). 7 parts of sodium tetrachloroaluminate, a by-product rich in sodium tetrachloroaluminate during the production of diethyl methylphosphonite, is slowly poured into the dissolving kettle for dissolution, and then solid-liquid separation is carried out. Take out the sodium chloride crystals and collect the solution;
[0054] (2) Add the collected solution to the reaction kettle, then add 0.5 part of ferric chloride and 1 part of hydrochloric acid, stir and mix for 15 minutes;
[0055] (3) Control the temperature of the reactor to be above 85°C; add 1 part of aluminum hydroxide and 2 parts of calcium metaaluminate in order for polymerization reaction;
[0056] (4), control the temperature to 100℃, keep the temperature for 75min;
[0057] (5) Separate after cooling, and the filtrate is the product of the invention.
[0058] Before the polymerization reaction, 0.02 parts of silicone oil was added as a defoaming agent.
[...
Embodiment 3
[0062] The present invention includes the following steps:
[0063] (1). 7 parts of sodium tetrachloroaluminate, a by-product rich in sodium tetrachloroaluminate during the production of diethyl methylphosphonite, is slowly poured into the dissolving kettle for dissolution, and then solid-liquid separation is carried out. Take out the sodium chloride crystals and collect the solution;
[0064] (2) Add the collected solution to the reaction kettle, then add 0.5 part of ferric chloride and 1 part of hydrochloric acid, stir and mix for 15 minutes;
[0065] (3) Control the temperature of the reactor to be above 85°C; add 1 part of aluminum hydroxide and 2 parts of calcium metaaluminate in order for polymerization reaction;
[0066] (4), control the temperature to 100℃, keep the temperature for 75min;
[0067] (5) Separate after cooling, and the filtrate is the product of the invention.
[0068] Before the polymerization reaction, 0.03 part of industrial white oil was added as a defoamer. T...
PUM
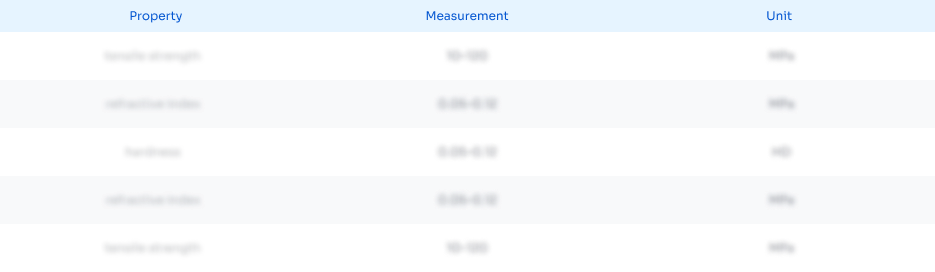
Abstract
Description
Claims
Application Information

- Generate Ideas
- Intellectual Property
- Life Sciences
- Materials
- Tech Scout
- Unparalleled Data Quality
- Higher Quality Content
- 60% Fewer Hallucinations
Browse by: Latest US Patents, China's latest patents, Technical Efficacy Thesaurus, Application Domain, Technology Topic, Popular Technical Reports.
© 2025 PatSnap. All rights reserved.Legal|Privacy policy|Modern Slavery Act Transparency Statement|Sitemap|About US| Contact US: help@patsnap.com