A supergravity method for preparing an aluminosilicate molecular sieve
A silica-alumina molecular sieve, supergravity technology, applied in chemical instruments and methods, crystalline aluminosilicate zeolite, chemical/physical/physical-chemical processes, etc. simple effect
- Summary
- Abstract
- Description
- Claims
- Application Information
AI Technical Summary
Problems solved by technology
Method used
Image
Examples
Embodiment 1
[0024] Take 1.3g of aluminum sulfate, 90g of silica sol, 3.5g of sodium chloride, 6g of sodium hydroxide, 100g of tetrapropylammonium hydroxide, and 200g of deionized water. Feed by peristaltic pump, pre-mixed at the supergravity level of 100-200g, the reaction temperature is 130°C, the reaction time is 12h, after the reaction in the supergravity reactor, the product is taken out. Transfer the synthesized product to a centrifuge tube, centrifuge at 3000-5000rpm, centrifuge for 5-10min, pour off the supernatant, and then wash with water 5-6 times until the pH of the solution is neutral. Calculating for 5 hours at the bottom to obtain silicon-aluminum molecular sieves, which are independently dispersed particles, the crystal appearance of the product is lateral stripes, the average particle size is 300nm, and the particle size distribution is 150-450nm.
Embodiment 2
[0026] Take 0.45g of aluminum sulfate, 50g of silica sol, 2g of sodium chloride, and 78g of tetrapropylammonium hydroxide. The peristaltic pump feeds, premixes at a supergravity level of 100-200g, the reaction temperature is 150°C, and the reaction time is 6h. After the reaction in the supergravity reactor is completed, the product is taken out. Transfer the synthesized product to a centrifuge tube, centrifuge at 3000-5000rpm, centrifuge for 5-10min, pour off the supernatant, and then wash with water 5-6 times until the pH of the solution is neutral. Calculating for 5 hours at the bottom to obtain the silica-alumina molecular sieve, which is independently dispersed in the shape of round or elliptical particles, with an average particle size of 400nm and a particle size distribution of 200-450nm.
Embodiment 3
[0028] Take 0.5g of aluminum sulfate, 60g of silica sol, 1.5g of sodium chloride, and 90g of tetrapropylammonium hydroxide. Feed by peristaltic pump, pre-mixed at the supergravity level of 100-200g, the reaction temperature is 130°C, the reaction time is 12h, after the reaction in the supergravity reactor, the product is taken out. Transfer the synthesized product to a centrifuge tube, centrifuge at 3000-5000rpm, centrifuge for 5-10min, pour off the supernatant, and then wash with water 5-6 times until the pH of the solution is neutral. Calculating for 5 hours at the bottom to obtain silica-alumina molecular sieves, which are independently dispersed particles, most of which are dumbbell-shaped structures composed of two circles, and the particle size range is 300-1000nm.
PUM
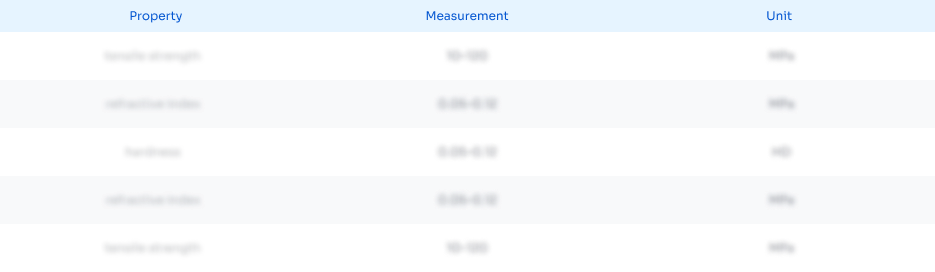
Abstract
Description
Claims
Application Information

- R&D
- Intellectual Property
- Life Sciences
- Materials
- Tech Scout
- Unparalleled Data Quality
- Higher Quality Content
- 60% Fewer Hallucinations
Browse by: Latest US Patents, China's latest patents, Technical Efficacy Thesaurus, Application Domain, Technology Topic, Popular Technical Reports.
© 2025 PatSnap. All rights reserved.Legal|Privacy policy|Modern Slavery Act Transparency Statement|Sitemap|About US| Contact US: help@patsnap.com