An Optimum Design Method of Grinding Wheel Dressing Amount Based on Controlled Cutting Thickness Distribution of Abrasive Grains
A technology of grinding wheel dressing and design methods, applied in the directions of grinding machine parts, design optimization/simulation, grinding/polishing equipment, etc.
- Summary
- Abstract
- Description
- Claims
- Application Information
AI Technical Summary
Problems solved by technology
Method used
Image
Examples
Embodiment 1
[0052] In this embodiment, the optimized design of the grinding amount is carried out with the goal of obtaining a good machined surface quality. The workpiece is No. 45 steel, and the surface roughness Ra of the processing result is expected to be less than 0.4um. The user has given the parameters of the abrasive grain on the surface of the grinding wheel. The grain size, position and edge height are all normal distributions. The parameters are: grain size N(550 ,0.25), position N(0.1,0.4), the blade height is N(67,0.15). The given processing amount is the grinding speed v s =45m / s, feed speed v w =20m / min, grinding depth a p It is 10um; the trimming amount is initially estimated to be 50um
[0053] Specific optimization design process:
[0054] (1) Set the target abrasive grain cutting thickness distribution according to the processing results, such as figure 1 The distribution 1 of the given grinding wheel is shown in 1; the abrasive particle parameters of the given gr...
PUM
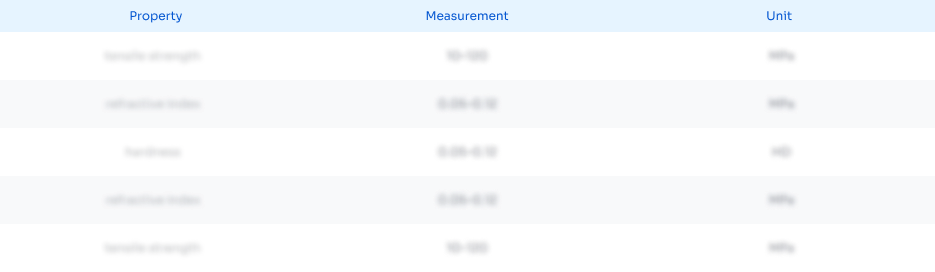
Abstract
Description
Claims
Application Information

- R&D
- Intellectual Property
- Life Sciences
- Materials
- Tech Scout
- Unparalleled Data Quality
- Higher Quality Content
- 60% Fewer Hallucinations
Browse by: Latest US Patents, China's latest patents, Technical Efficacy Thesaurus, Application Domain, Technology Topic, Popular Technical Reports.
© 2025 PatSnap. All rights reserved.Legal|Privacy policy|Modern Slavery Act Transparency Statement|Sitemap|About US| Contact US: help@patsnap.com