Method for improving deep plating capacity of electrocoppering
A technology of electroplating copper and electroplating copper layers, which is applied in the direction of electrolytic process, electrolytic components, cells, etc., can solve the problems of reduced production capacity, board surface quality problems, waste of resources, etc., and achieve the effect of improving deep plating ability
- Summary
- Abstract
- Description
- Claims
- Application Information
AI Technical Summary
Problems solved by technology
Method used
Examples
Embodiment 1
[0023] A method for improving electroplated copper deep plating ability, comprising the following steps:
[0024] A. Configure the electroplating solution, the electroplating solution includes,
[0025] Copper sulfate 150g / L, sulfuric acid 380g / L, sodium nitrite 6g / L, 3-oxocyclobutane carboxylic acid 17g / L, manganese disodium edetate 3g / L, 4-methyl-2 - sodium oxopentanoate 10g / L, brightener 6g / L, smoothing agent 6g / L, modifier 3g / L, and the balance is water;
[0026] B. Inject the electroplating solution into the electroplating tank, and put the circuit substrate vertically into the electroplating tank;
[0027] C. Control the temperature of the electroplating solution at 52°C, conduct electroplating with electricity, and control the current density at 16A / dm 2 ;
[0028] D. When the thickness of the electroplated copper layer increases to 55% of the target thickness, the temperature of the electroplating solution is raised to 65°C, and the current density is reduced to 5.5...
Embodiment 2
[0040] A method for improving electroplated copper deep plating ability, comprising the following steps:
[0041] A. Configure the electroplating solution, the electroplating solution includes,
[0042] Copper sulfate 150g / L, sulfuric acid 380g / L, sodium nitrite 6g / L, 3-oxocyclobutane carboxylic acid 17g / L, manganese disodium edetate 3g / L, 4-methyl-2 - sodium oxopentanoate 10g / L, brightener 6g / L, smoothing agent 6g / L, modifier 3g / L, and the balance is water;
[0043] B. Inject the electroplating solution into the electroplating tank, and put the circuit substrate vertically into the electroplating tank;
[0044] C. Control the temperature of the electroplating solution at 52°C, conduct electroplating with electricity, and control the current density at 16A / dm 2 ;
[0045] D. When the thickness of the electroplated copper layer increases to 55% of the target thickness, the temperature of the electroplating solution is raised to 65°C, and the current density is reduced to 5.5...
Embodiment 3
[0057] A method for improving electroplated copper deep plating ability, comprising the following steps:
[0058] A. Configure the electroplating solution, the electroplating solution includes,
[0059] Copper sulfate 150g / L, sulfuric acid 380g / L, sodium nitrite 6g / L, 3-oxocyclobutane carboxylic acid 17g / L, manganese disodium edetate 3g / L, 4-methyl-2 -Sodium oxopentanoate 10g / L, brightener 6g / L, smoothing agent 6g / L, modifier 3g / L, also includes 1-ethyl-3-methylimidazole potassium hexafluorophosphate 6g / L, remaining amount of water;
[0060] B. Inject the electroplating solution into the electroplating tank, and put the circuit substrate vertically into the electroplating tank;
[0061] C. Control the temperature of the electroplating solution at 52°C, conduct electroplating with electricity, and control the current density at 16A / dm 2 ;
[0062] D. When the thickness of the electroplated copper layer increases to 55% of the target thickness, the temperature of the electro...
PUM
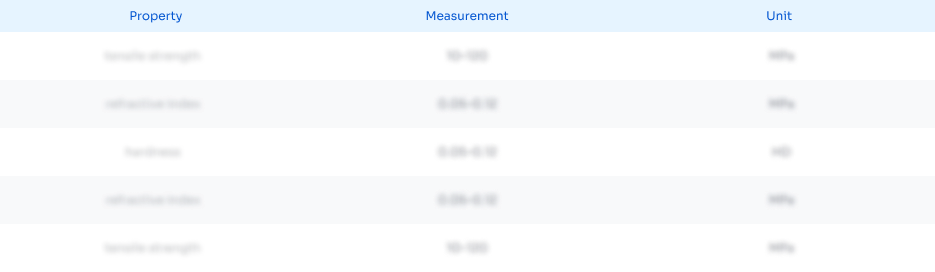
Abstract
Description
Claims
Application Information

- Generate Ideas
- Intellectual Property
- Life Sciences
- Materials
- Tech Scout
- Unparalleled Data Quality
- Higher Quality Content
- 60% Fewer Hallucinations
Browse by: Latest US Patents, China's latest patents, Technical Efficacy Thesaurus, Application Domain, Technology Topic, Popular Technical Reports.
© 2025 PatSnap. All rights reserved.Legal|Privacy policy|Modern Slavery Act Transparency Statement|Sitemap|About US| Contact US: help@patsnap.com