Composite 3D printing material and preparation method thereof
A 3D printing and raw material technology, applied in the field of 3D printing materials, can solve problems such as 3D printing is not easy, pungent smell, cracking, etc., and achieve the effects of good toughness, improved tensile strength, and improved heat resistance
- Summary
- Abstract
- Description
- Claims
- Application Information
AI Technical Summary
Problems solved by technology
Method used
Examples
Embodiment 1
[0019] A composite 3D printing material proposed by the present invention comprises the following raw materials in parts by weight: 30 parts of photosensitive resin, 15 parts of modified aramid pulp, 12 parts of talcum powder, 8 parts of pigment, 5 parts of polycaprolactone, fat 2 parts of dibasic acid ester, 6 parts of ethyl acetate, 2 parts of lubricant, 1 part of coupling agent;
[0020] Among them, the preparation of the modified aramid pulp is as follows: mix 0.5 parts of silane coupling agent and 5 parts of absolute ethanol, then add 10 parts of aramid pulp, ultrasonically disperse for 0.5 h, then carry out mechanical stirring for 4 h, and then use HCl Adjust the pH to 4, adjust the reaction temperature to 50°C, and ultrasonically disperse for 1 hour to obtain a uniform aramid pulp dispersion, centrifuge, wash with distilled water until the pH is neutral, and dry to obtain the modified aramid pulp;
[0021] Wherein, the lubricant is a mixture of white mineral oil, silico...
Embodiment 2
[0027] A composite 3D printing material proposed by the present invention comprises the following raw materials in parts by weight: 50 parts of photosensitive resin, 30 parts of modified aramid pulp, 20 parts of talcum powder, 15 parts of pigment, 10 parts of polycaprolactone, fat 5 parts of family dibasic acid ester, 12 parts of ethyl acetate, 5 parts of butyl stearate, 4 parts of coupling agent;
[0028] Among them, the preparation of the modified aramid pulp is as follows: mix 1 part of silane coupling agent and 10 parts of absolute ethanol, then add 20 parts of aramid pulp, ultrasonically disperse for 1 hour, then carry out mechanical stirring for 5 hours, and then use HCl to adjust Adjust the pH to 5, adjust the reaction temperature to 55°C, and ultrasonically disperse for 3 hours to obtain a uniform dispersion of aramid pulp, centrifuge, wash with distilled water until the pH is neutral, and dry to obtain the modified aramid pulp.
[0029] The present invention also prop...
Embodiment 3
[0034] A composite 3D printing material proposed by the present invention comprises the following raw materials in parts by weight: 40 parts of photosensitive resin, 22 parts of modified aramid pulp, 16 parts of talcum powder, 11 parts of pigment, 8 parts of polycaprolactone, fat 3.5 parts of dibasic acid ester, 9 parts of ethyl acetate, 3.5 parts of ethylene bis stearamide, 2.5 parts of coupling agent;
[0035] Among them, the preparation of modified aramid pulp is as follows: mix 0.8 parts of silane coupling agent and 8 parts of absolute ethanol, then add 15 parts of aramid pulp, ultrasonically disperse for 0.7 hours, and then perform mechanical stirring for 4.5 hours, and then use Adjust the pH to 4.5 with HCl, adjust the reaction temperature to 55°C, and ultrasonically disperse for 3 hours to obtain a uniform dispersion of aramid pulp, centrifuge, wash with distilled water until the pH is neutral, and dry to obtain the modified aramid pulp.
[0036] The present invention a...
PUM
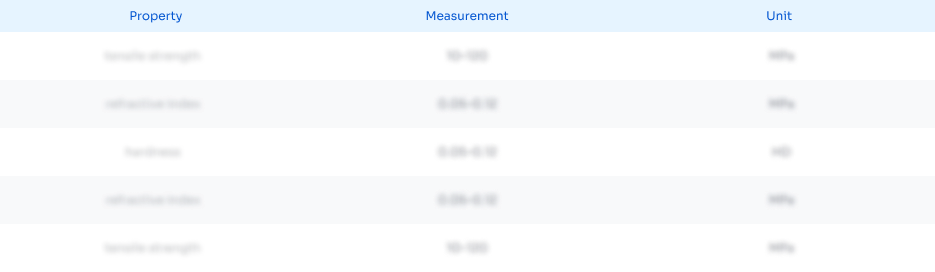
Abstract
Description
Claims
Application Information

- Generate Ideas
- Intellectual Property
- Life Sciences
- Materials
- Tech Scout
- Unparalleled Data Quality
- Higher Quality Content
- 60% Fewer Hallucinations
Browse by: Latest US Patents, China's latest patents, Technical Efficacy Thesaurus, Application Domain, Technology Topic, Popular Technical Reports.
© 2025 PatSnap. All rights reserved.Legal|Privacy policy|Modern Slavery Act Transparency Statement|Sitemap|About US| Contact US: help@patsnap.com