Hyperbranched polyamidoamine modified plant fiber reinforced polypropylene micro foaming material and preparation method thereof
A plant fiber and polyamidoamine technology, which is applied in the field of hyperbranched polyamidoamine modified plant fiber reinforced polypropylene micro-foaming materials and its preparation, can solve the problems of difficult dispersion, poor compatibility of non-polar polymers, and influence on fiber Comprehensive properties of composite materials and other issues, to achieve the effect of uniform and fine cells, improve compatibility, and fine cells
- Summary
- Abstract
- Description
- Claims
- Application Information
AI Technical Summary
Problems solved by technology
Method used
Image
Examples
Embodiment 1
[0033] In this embodiment, the polypropylene composite material is composed of the following raw materials in parts by weight:
[0034]
[0035]
[0036] The hyperbranched polyamidoamine modified plant fiber reinforced polypropylene micro-foaming composite material is composed of 98wt% polypropylene composite material and 2wt% chemical foaming agent.
[0037] Concrete preparation method comprises the following steps:
[0038] (1) Weigh 96 parts of jute fiber and add it to the ethanol aqueous solution with a volume ratio of 90:10, soak at room temperature for 30 minutes, slowly add 4 parts of γ-glycidyl etheroxypropyl trimethoxysilane, heat up to 50-60°C and stir at a constant temperature 24-48h, washed 5 times with dehydrated ethanol, and vacuum-dried the product at 80°C for 24-48h to obtain modified jute fiber;
[0039] (2) Soak the modified jute fiber prepared in step (1) in ethanol for 30min, slowly add 3 parts of hyperbranched polyamidoamine, heat up to 70°C and sti...
Embodiment 2
[0043] In this embodiment, the polypropylene composite material is composed of the following raw materials in parts by weight:
[0044]
[0045]
[0046] The hyperbranched polyamidoamine modified plant fiber reinforced polypropylene micro-foaming composite material is composed of 97wt% polypropylene composite material and 3wt% chemical foaming agent.
[0047] Concrete preparation method comprises the following steps:
[0048] (1) Weigh 93 parts of ramie fiber and add it to ethanol water solution with a volume ratio of 90:10, soak at room temperature for 20 minutes, slowly add 7 parts of γ-glycidyl etheroxypropylmethyldiethoxysilane, heat up to 55°C and stir at constant temperature 36h, washed 4 times with dehydrated ethanol, and vacuum-dried the product at 60°C for 24h-48h to obtain modified ramie fibers;
[0049] (2) Soak the modified ramie fiber prepared in step (1) in ethanol for 20 minutes, slowly add 5 parts of hyperbranched polyamidoamine, heat up to 65°C and stir...
Embodiment 3
[0053] In this embodiment, the polypropylene composite material is composed of the following raw materials in parts by weight:
[0054]
[0055]
[0056] The hyperbranched polyamidoamine modified plant fiber reinforced polypropylene micro-foaming composite material is composed of 98wt% polypropylene composite material and 2wt% chemical foaming agent.
[0057] Concrete preparation method comprises the following steps:
[0058] (1) Weigh 90 parts of flax fiber and add it to an ethanol aqueous solution with a volume ratio of 90:10, soak at room temperature for 10 minutes, slowly add 10 parts of γ-glycidyloxypropyltrimethoxysilane, heat up to 50°C and stir at a constant temperature for 24 hours, Washing with dehydrated ethanol for 3 times, vacuum-drying the product at 50°C for 24 hours, finally obtaining modified flax fiber;
[0059] (2) Soak the modified jute fiber prepared in step (1) in ethanol for 10 minutes, slowly add 10 parts of hyperbranched polyamidoamine, heat up ...
PUM
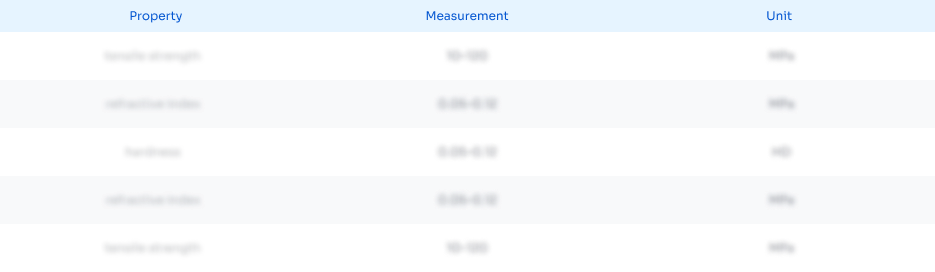
Abstract
Description
Claims
Application Information

- Generate Ideas
- Intellectual Property
- Life Sciences
- Materials
- Tech Scout
- Unparalleled Data Quality
- Higher Quality Content
- 60% Fewer Hallucinations
Browse by: Latest US Patents, China's latest patents, Technical Efficacy Thesaurus, Application Domain, Technology Topic, Popular Technical Reports.
© 2025 PatSnap. All rights reserved.Legal|Privacy policy|Modern Slavery Act Transparency Statement|Sitemap|About US| Contact US: help@patsnap.com