Production method and production system of dimethyl dicarbonate
A technology of dimethyl dicarbonate and production method, which is applied in the direction of purification/separation of carbonate/haloformate, preparation of carbonate/haloformate, chemical instruments and methods, etc., and can solve the increase target Product and water contact time, reducing reaction conversion rate and other issues, to achieve the effect of increasing the yield of target substances, increasing conversion rate, and shortening the process flow
- Summary
- Abstract
- Description
- Claims
- Application Information
AI Technical Summary
Problems solved by technology
Method used
Image
Examples
Embodiment 1
[0028] A kind of production method of dimethyl dicarbonate, such as figure 1shown, including the following steps:
[0029] (1) Add methyl chloroformate, solvent and catalyst into feeding tank 1 in a mass ratio of 1:1:0.02 and mix evenly to obtain a mixed reaction material; wherein the solvent is selected from dimethyl carbonate, methylene chloride and xylene At least one of the catalysts selected from dodecyl dimethyl benzyl ammonium chloride, three - (dodecyl) methyl ammonium chloride, tris - (tetradecyl) methyl ammonium chloride and At least one of tetra-(octaalkyl)ammonium chloride;
[0030] (2) Send the mixed reaction materials into the reaction buffer tank 2 with oil-water separation function, control the temperature in the reaction buffer tank 2 to be 0-15°C, and send the mixed reaction materials through the material circulation pump 8 and the Venturi tube 4 in turn In the static mixing reactor 5, the sodium hydroxide solution that will come from the mass concentration...
Embodiment 2
[0035] With above-mentioned embodiment 1, its difference is:
[0036] In step (1), the mass ratio of methyl chloroformate, solvent and catalyst is 1:0.5:0.005;
[0037] In step (2), the molar ratio of sodium hydroxide to methyl chloroformate is 1:1.0;
[0038] In step (3), the absolute pressure of the low-vacuum evaporator 6 is controlled to be 10 kpa, and the evaporation temperature is 35°C;
[0039] In step (4), the absolute pressure of the high vacuum evaporator 7 is controlled to be 190 pa, the distillation temperature is 25°C, and the purity of the obtained dimethyl dicarbonate product is 99.90%.
Embodiment 3
[0041] With above-mentioned embodiment 1, its difference is:
[0042] In step (1), the mass ratio of methyl chloroformate, solvent and catalyst is 1:0.5:0.005;
[0043] In step (2), the molar ratio of sodium hydroxide to methyl chloroformate is 1:1.0;
[0044] In step (3), the absolute pressure of the low-vacuum evaporator 6 is controlled to be 3kpa, and the evaporation temperature is 10°C;
[0045] In step (4), the absolute pressure of the high-vacuum evaporator 7 is controlled to 60 pa, the distillation temperature is 10°C, and the purity of the obtained dimethyl dicarbonate product is 99.90%.
PUM
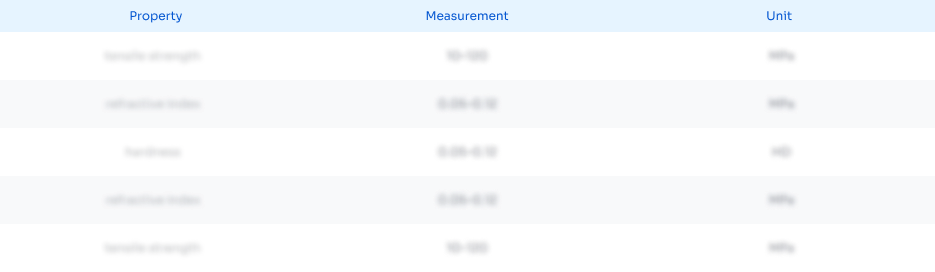
Abstract
Description
Claims
Application Information

- R&D
- Intellectual Property
- Life Sciences
- Materials
- Tech Scout
- Unparalleled Data Quality
- Higher Quality Content
- 60% Fewer Hallucinations
Browse by: Latest US Patents, China's latest patents, Technical Efficacy Thesaurus, Application Domain, Technology Topic, Popular Technical Reports.
© 2025 PatSnap. All rights reserved.Legal|Privacy policy|Modern Slavery Act Transparency Statement|Sitemap|About US| Contact US: help@patsnap.com