Warping machine warp beam transfer robot and control method thereof
A control method and warping machine technology, applied in the direction of program control of manipulators, manipulators, manufacturing tools, etc., can solve the problems of low efficiency of warp beams of warping machines, high labor intensity of workers, and potential safety hazards, and achieve a reasonable and effective control method. order, realize automatic production, and avoid the effect of collision accidents
- Summary
- Abstract
- Description
- Claims
- Application Information
AI Technical Summary
Problems solved by technology
Method used
Image
Examples
Embodiment 2
[0025] Embodiment 2, a warp beam transfer robot, the electromagnetic navigation system includes metal wires buried in the walking section 5, and the metal wire is loaded with a guiding frequency, and the warp beam transfer robot 7 recognizes the Guidance frequency for navigation; the laser positioning system includes a laser transmitter and a laser receiver arranged on the beam transfer robot 7 of the warping machine, and the laser transmitter includes a first laser transmitter 71, a second laser transmitter 72, and a laser transmitter 71. The receiver comprises a first laser receiver and a second laser receiver. Two reflection plates are arranged on both sides of the headstock of the warping machine 8. The first laser receiver and the second laser receiver are all arranged on the reflection plates. The first laser receiver Both the receiver and the second laser receiver are used to receive the laser signal sent by the first laser transmitter 71 and the laser signal sent by the...
Embodiment 3
[0026] Embodiment 3, a method for controlling a warp beam transfer robot of a warping machine, comprising the following steps:
[0027] Step 1: Take the empty shaft. When the warp yarns on the warping machine 8 are about to be full, the control system starts the electromagnetic navigation system and the driving system, and the warping machine warp beam transfer robot 7 is driven by the driving system and carried out by the electromagnetic navigation system. Navigate from the standby charging position 1 to the empty shaft taking position 2, take out the empty shaft in the empty shaft storehouse 9 and place the empty shaft on the empty shaft temporary storage position on the warping machine warp beam transfer robot 7.
[0028]Step 2: Send the empty shaft. After the warp beam transfer robot 7 loads the empty shaft, the control system starts the electromagnetic navigation system and the drive system again, and the warp beam transfer robot 7 is driven by the drive system and driven ...
Embodiment 4
[0033] Embodiment 4, a control method of a warping beam transfer robot, the first laser emitter 71 is arranged at the front end of the warping beam transfer robot 7 and the coordinates are A(x 1 ,y 1 ), the second laser emitter 72 is arranged on the rear end of the beam transfer robot 7 of the warping machine and the coordinates are B(x 2 ,y 2 ), the front and back of coordinate A and coordinate B correspond and the height of coordinate A is lower than the height of coordinate B, and a reflecting plate 73 is arranged on the left side of warping machine 8 and coordinate is R 1 (x a ,y a ), another reflecting plate 74 is arranged on the right side of the warping machine 8 and the coordinates are R 2 (x b ,y a ). When the laser receiver receives the laser signals of the first laser transmitter 71 and the second laser transmitter 72 respectively, the distance l between the two laser transmitters and the two laser receivers can be obtained sequentially through the laser rang...
PUM
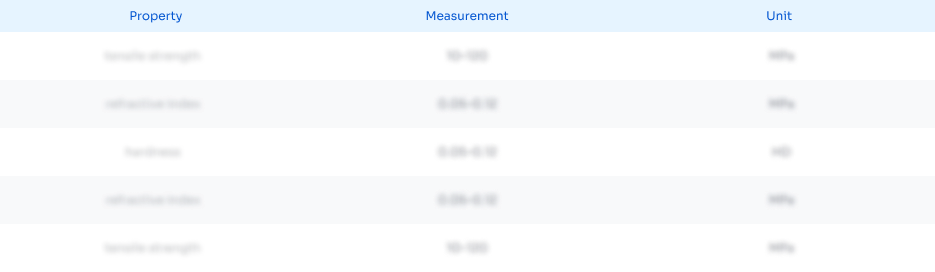
Abstract
Description
Claims
Application Information

- R&D Engineer
- R&D Manager
- IP Professional
- Industry Leading Data Capabilities
- Powerful AI technology
- Patent DNA Extraction
Browse by: Latest US Patents, China's latest patents, Technical Efficacy Thesaurus, Application Domain, Technology Topic, Popular Technical Reports.
© 2024 PatSnap. All rights reserved.Legal|Privacy policy|Modern Slavery Act Transparency Statement|Sitemap|About US| Contact US: help@patsnap.com