Formation method for alleviating wavy edges of low-pressure forming foils
A chemical forming method and forming foil technology, applied in the direction of electrolytic capacitors, coatings, capacitor electrodes, etc., can solve the problems of affecting downstream cutting, small effective use area, etc., to achieve flat utilization, improve product consistency, and central dispersion. small effect
- Summary
- Abstract
- Description
- Claims
- Application Information
AI Technical Summary
Problems solved by technology
Method used
Image
Examples
Embodiment 1
[0018] Example 1: Pretreatment: Put the low-pressure corrosion foil into a mixed aqueous solution of 5wt% γ-butyrolactone and 0.2wt% maleic acid at a temperature of 40°C for 5 minutes; put the pretreated aluminum foil in 7wt% hexanoic acid Ammonium diacid and 0.05wt% maleic acid solution, temperature 70°C, current density 20mA / cm 2 , the voltage is 5v, and anodized for 5 minutes to obtain a primary formed foil; the primary formed foil is placed in a solution of 7wt% ammonium adipate and 0.05wt% maleic acid at a temperature of 70°C and a current density of 20mA / cm 2 , the voltage is 10v, and anodized for 5min to obtain a secondary formed foil; the secondary formed foil is placed in a solution of 7wt% ammonium adipate and 0.05wt% maleic acid at a temperature of 70°C and a current density of 20mA / cm 2 , the voltage is 15v, and anodized for 5min to obtain a three-stage formed foil; place the three-stage formed foil in a solution of 7wt% ammonium adipate and 0.01wt% maleic acid at ...
Embodiment 2
[0019] Example 2: Pretreatment: Put the low-pressure corrosion foil into a mixed aqueous solution of 15wt% γ-butyrolactone and 1wt% maleic acid at a temperature of 50°C for 3 minutes; put the pretreated aluminum foil in 10wt% adipic di ammonium phosphate and 0.1wt% maleic acid solution, temperature 60°C, current density 50mA / cm 2 , the voltage is 10v, and anodized for 7 minutes to obtain a primary formed foil; the primary formed foil is placed in a solution of 10wt% ammonium adipate and 0.1wt% maleic acid at a temperature of 60°C and a current density of 50mA / cm 2 , the voltage is 20v, and anodized for 7 minutes to obtain a secondary formed foil; the secondary formed foil is placed in a solution of 10wt% ammonium adipate and 0.1wt% maleic acid at a temperature of 60°C and a current density of 50mA / cm 2 , the voltage is 30v, and anodized for 7min to obtain a tertiary formed foil; place the tertiary formed foil in a solution of 10wt% ammonium adipate and 0.01wt% maleic acid at a...
Embodiment 3
[0020] Example 3: Pretreatment: Put the low-pressure corrosion foil into a mixed aqueous solution of 30wt% γ-butyrolactone and 2wt% maleic acid at a temperature of 60°C for 1 min; put the pretreated aluminum foil in 15wt% adipic di ammonium phosphate and 0.5wt% maleic acid solution, temperature 80°C, current density 100mA / cm 2 , the voltage is 20v, and anodized for 10min to obtain a primary formed foil; the primary formed foil is placed in a solution of 15wt% ammonium adipate and 0.5wt% maleic acid at a temperature of 80°C and a current density of 100mA / cm 2, the voltage is 40v, and anodized for 10min to obtain a secondary formed foil; the secondary formed foil is placed in a solution of 15wt% ammonium adipate and 0.5wt% maleic acid at a temperature of 80°C and a current density of 100mA / cm 2 , the voltage is 60v, and anodized for 10min to obtain a three-stage formed foil; place the three-stage formed foil in a solution of 15wt% ammonium adipate and 0.01wt% maleic acid at a te...
PUM
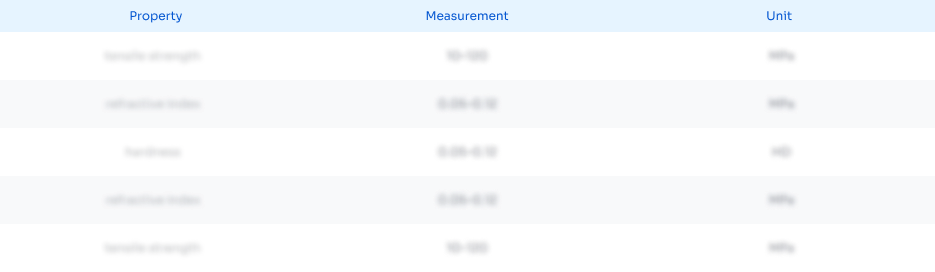
Abstract
Description
Claims
Application Information

- R&D Engineer
- R&D Manager
- IP Professional
- Industry Leading Data Capabilities
- Powerful AI technology
- Patent DNA Extraction
Browse by: Latest US Patents, China's latest patents, Technical Efficacy Thesaurus, Application Domain, Technology Topic, Popular Technical Reports.
© 2024 PatSnap. All rights reserved.Legal|Privacy policy|Modern Slavery Act Transparency Statement|Sitemap|About US| Contact US: help@patsnap.com