A new energy vehicle light and durable motor casing manufacturing process
A new energy vehicle and manufacturing process technology, applied in the field of new energy auto parts, can solve the problems of high-strength steel plate stamping performance decline, mechanical, weight heat treatment performance is not perfect, affect the process cost, etc., to improve fatigue strength and reduce production The effect of difficulty and excellent mechanical properties
- Summary
- Abstract
- Description
- Claims
- Application Information
AI Technical Summary
Problems solved by technology
Method used
Examples
Embodiment 1
[0023] A manufacturing process for a lightweight and durable motor casing for a new energy vehicle, comprising the following steps:
[0024] (1) Casting: Make and install the sand core and casting mold according to the overall structure of the motor casing, put the aluminum ingot into the melting furnace for melting, and after melting at 710~725°C, the air pump drives the molten aluminum to flow into the casting mold through the conduit Middle; after casting, add liquid aluminum to the riser in time to feed the shrinkage, and cool slowly to below 100°C to obtain a motor housing with a sand core; the aluminum alloy used for the casting is cast aluminum alloy, preferably ZL104, ZL108 , one of ZL109, ZL110; the slow cooling method adopts air cooling, and the time is 1.5h;
[0025] (2) Cleaning out of the box: loosen the molding sand at the riser with an air shovel, separate the upper and lower boxes, take out the casting in time, clean the sand core with the air shovel, deburr, p...
Embodiment 2
[0032] A manufacturing process for a lightweight and durable motor casing for a new energy vehicle, comprising the following steps:
[0033] (1) Casting: Make and install the sand core and casting mold according to the overall structure of the motor casing, put the aluminum ingot into the melting furnace for melting, and after melting at 710~725°C, the air pump drives the molten aluminum to flow into the casting mold through the conduit Middle; after casting, add liquid aluminum to the riser in time to feed the shrinkage, and cool slowly to below 100°C to obtain a motor housing with a sand core; the aluminum alloy used for the casting is cast aluminum alloy, preferably ZL104, ZL108 , one of ZL109, ZL110; the slow cooling method adopts air cooling, and the time is 1.6h;
[0034] (2) Cleaning out of the box: loosen the molding sand at the riser with an air shovel, separate the upper and lower boxes, take out the casting in time, clean the sand core with the air shovel, deburr, p...
Embodiment 3
[0041] A manufacturing process for a lightweight and durable motor casing for a new energy vehicle, comprising the following steps:
[0042] (1) Casting: Make and install the sand core and casting mold according to the overall structure of the motor casing, put the aluminum ingot into the melting furnace for melting, and after melting at 710~725°C, the air pump drives the molten aluminum to flow into the casting mold through the conduit Middle; after casting, add liquid aluminum to the riser in time to feed the shrinkage, and cool slowly to below 100°C to obtain a motor housing with a sand core; the aluminum alloy used for the casting is cast aluminum alloy, preferably ZL104, ZL108 , one of ZL109, ZL110; the slow cooling method adopts air cooling, and the time is 1.5h;
[0043] (2) Cleaning out of the box: loosen the molding sand at the riser with an air shovel, separate the upper and lower boxes, take out the casting in time, clean the sand core with the air shovel, deburr, p...
PUM
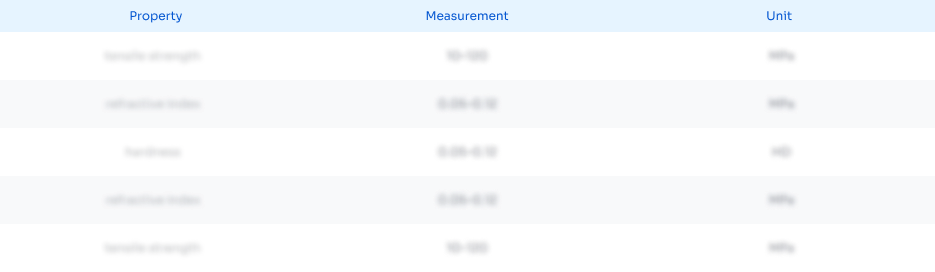
Abstract
Description
Claims
Application Information

- R&D
- Intellectual Property
- Life Sciences
- Materials
- Tech Scout
- Unparalleled Data Quality
- Higher Quality Content
- 60% Fewer Hallucinations
Browse by: Latest US Patents, China's latest patents, Technical Efficacy Thesaurus, Application Domain, Technology Topic, Popular Technical Reports.
© 2025 PatSnap. All rights reserved.Legal|Privacy policy|Modern Slavery Act Transparency Statement|Sitemap|About US| Contact US: help@patsnap.com