Rudder surface manufacturing method with aspect ratio being more than 9 times
A manufacturing method and aspect ratio technology, applied in the aviation field, can solve problems such as large deformation of the rudder surface, difficulty in controlling the weight of the rudder surface, and poor deflection angle accuracy
- Summary
- Abstract
- Description
- Claims
- Application Information
AI Technical Summary
Problems solved by technology
Method used
Image
Examples
Embodiment 1
[0045]Example 1. Put the clamped mold into the oven, heat the room temperature to 105°C with the furnace, keep it warm for 15 minutes, continue to raise the temperature to 160° C, and keep it warm for 3 minutes; after coming out of the oven, dip the upper and lower molds with cotton cloth, and the mold temperature drops to 40 ℃~60℃; disassemble the mold, and demould the overall foaming component; clean the upper and lower molds of the aileron, and wrap the carbon fiber cloth with hand brush (or pre-impregnated) epoxy resin in the mold to complete the inner lining of step 10 Foaming parts and mold closing; the mold enters the oven again, heats up to 105°C with the furnace, and keeps warm for 1.6h; after it comes out of the oven, it is air-cooled to room temperature, and after the mold is disassembled, the rudder surface is demoulded, and all sides are trimmed to complete the manufacture of the rudder surface Work.
Embodiment 2
[0046] Example 2: Put the clamped mold into the oven, heat the room temperature to 92°C with the furnace, keep it warm for 11 minutes, continue to raise the temperature to 145° C, and keep it warm for 1.5 minutes; 40°C~60°C; disassemble the mold, and demould the overall foaming component; clean the upper and lower molds of the aileron, and wrap the inner lining of step 10 with hand-brushed (or pre-impregnated) epoxy resin carbon fiber cloth in the mold Foaming parts and mold closing; the mold enters the oven again, heats up to 92°C with the furnace, and keeps warm for 1.4 hours; after it comes out of the oven, it is air-cooled to room temperature, and after the mold is disassembled, the rudder surface is demoulded, and all sides are trimmed to complete the manufacture of the rudder surface Work.
PUM
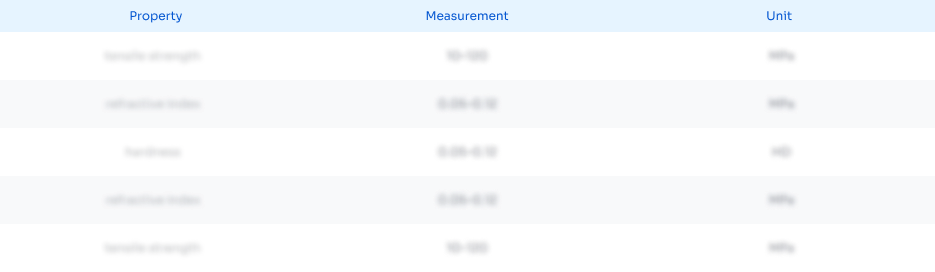
Abstract
Description
Claims
Application Information

- R&D
- Intellectual Property
- Life Sciences
- Materials
- Tech Scout
- Unparalleled Data Quality
- Higher Quality Content
- 60% Fewer Hallucinations
Browse by: Latest US Patents, China's latest patents, Technical Efficacy Thesaurus, Application Domain, Technology Topic, Popular Technical Reports.
© 2025 PatSnap. All rights reserved.Legal|Privacy policy|Modern Slavery Act Transparency Statement|Sitemap|About US| Contact US: help@patsnap.com