Carbon oil printing process of circuit board
A circuit board, carbon oil technology, applied in the direction of conductive pattern formation, etc., can solve the problems of carbon oil open circuit, carbon oil short circuit, carbon oil accumulating oil short circuit, etc., to prevent carbon oil open circuit or carbon oil accumulating oil short circuit, oiliness Complete and good quality results
- Summary
- Abstract
- Description
- Claims
- Application Information
AI Technical Summary
Problems solved by technology
Method used
Examples
Embodiment
[0021] The manufacturing method of a circuit board shown in this embodiment includes a carbon oil printing process for the carbon oil patterns at 90° to each other and the carbon oil pattern spacing <0.45mm, including the following processing steps:
[0022] (1) Cutting: cut out the core board according to the panel size 320mm×420mm, the thickness of the core board is 0.5mm, and the thickness of the outer copper surface of the core board is 0.5OZ.
[0023] (2), making the inner layer circuit (negative film process): transfer the inner layer graphics, coat the photosensitive film with a vertical coating machine, the film thickness of the photosensitive film is controlled to 8 μm, use a fully automatic exposure machine, and use a 5-6 grid exposure ruler ( 21-grid exposure ruler) to complete the exposure of the inner layer circuit; inner layer etching, etch out the circuit pattern on the core board after exposure and development, and measure the inner layer line width to 3mil; inn...
PUM
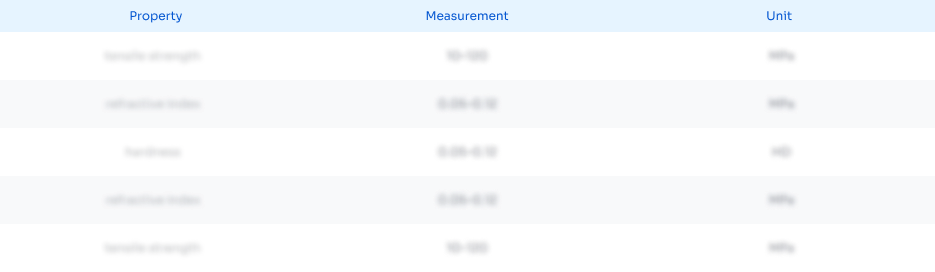
Abstract
Description
Claims
Application Information

- R&D Engineer
- R&D Manager
- IP Professional
- Industry Leading Data Capabilities
- Powerful AI technology
- Patent DNA Extraction
Browse by: Latest US Patents, China's latest patents, Technical Efficacy Thesaurus, Application Domain, Technology Topic, Popular Technical Reports.
© 2024 PatSnap. All rights reserved.Legal|Privacy policy|Modern Slavery Act Transparency Statement|Sitemap|About US| Contact US: help@patsnap.com