Preparation method of heating chip with fused nanometer carbon fibers and wood fibers
A nano-carbon fiber and heating chip technology, which is applied in the direction of electric heating devices, ohmic resistance heating, heating element materials, etc., can solve the problems of poor resistance uniformity, insufficient fusion of carbon materials and plant fiber materials, etc., and achieve resistance uniformity enhanced effect
- Summary
- Abstract
- Description
- Claims
- Application Information
AI Technical Summary
Problems solved by technology
Method used
Examples
Embodiment 1
[0028] A method for preparing a heating chip fused with carbon nanofibers and wood fibers, comprising the following steps:
[0029] A. Put 1 kg of conductive carbon fiber into the vortex disperser, put 100 kg of clean water, add 300g of water-based dispersant, turn on the vortex disperser, and work for 1.5 hours;
[0030] B. Then add a sodium hydroxide solution with a mass fraction of 40%, and the addition amount is 120g, and then close the disperser after working for 0.5 hours;
[0031] C. While the disperser is working for the first time, put 50 kg of plant fiber into another vortex disperser, put 500 kg of clean water, and start the disperser to disperse;
[0032] D. Take out the carbon fiber that has been processed in the previous disperser, and pour it into the disperser that puts the plant fiber in the back; then turn on the disperser and work for 2 hours;
[0033] E. Then put 5 kg of nano-scale graphite conductive particles and work for another 2 hours;
[0034] F. Th...
Embodiment 2
[0036] A method for preparing a heating chip fused with carbon nanofibers and wood fibers, comprising the following steps:
[0037] A. Put 1 kg of conductive carbon fiber into the vortex disperser, put 80 kg of clean water, add 500g of water-based dispersant, turn on the vortex disperser, and work for 1 hour;
[0038] B. Then add a sodium hydroxide solution with a mass fraction of 30%, and the addition amount is 450g, and then close the disperser after working for 0.8 hours;
[0039] C. While the disperser is working for the first time, put 30 kg of plant fiber into another vortex disperser, put 450 kg of clean water, and start the disperser to disperse;
[0040] D. Take out the carbon fiber that has been processed in the previous disperser, and pour it into the disperser that puts the plant fiber in the back; then turn on the disperser and work for 2.5 hours;
[0041] E. Then put 3 kg of nano-scale graphite conductive particles, and then work for 2.5 hours;
[0042] F. Then...
Embodiment 3
[0044] A method for preparing a heating chip fused with carbon nanofibers and wood fibers, comprising the following steps:
[0045] A. Put 1 kg of conductive carbon fiber into the vortex disperser, put 120 kg of clean water, add 100g of water-based dispersant, turn on the vortex disperser, and work for 2 hours;
[0046] B. Then add a sodium hydroxide solution with a mass fraction of 60%, and the addition amount is 80g, and then close the disperser after working for 0.2 hours;
[0047] C. While the disperser is working for the first time, put 80 kg of plant fibers into another vortex disperser, put 640 kg of clean water, and start the disperser to disperse;
[0048] D. Take out the carbon fiber that has been processed in the previous disperser, and pour it into the disperser that puts the plant fiber in the back; then turn on the disperser and work for 1.5 hours;
[0049] E. Then put 6 kg of nano-scale graphite conductive particles, and then work for 1.5 hours;
[0050] F. Th...
PUM
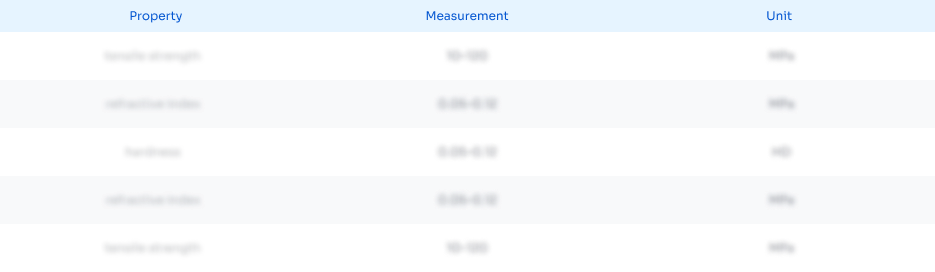
Abstract
Description
Claims
Application Information

- Generate Ideas
- Intellectual Property
- Life Sciences
- Materials
- Tech Scout
- Unparalleled Data Quality
- Higher Quality Content
- 60% Fewer Hallucinations
Browse by: Latest US Patents, China's latest patents, Technical Efficacy Thesaurus, Application Domain, Technology Topic, Popular Technical Reports.
© 2025 PatSnap. All rights reserved.Legal|Privacy policy|Modern Slavery Act Transparency Statement|Sitemap|About US| Contact US: help@patsnap.com