Co-curing preparation method of composite material/metal laminated-structure composite tube
A technology of composite materials and metal lamination, applied in the direction of shafts, shafts and bearings, mechanical equipment, etc., can solve the problems of short co-curing molding process cycle, unguaranteed matching of metal inner diameter, low cost, etc., to achieve fast and low cost. Cost-effective manufacturing, avoidance of machining processes, and effects of post-curing processes
- Summary
- Abstract
- Description
- Claims
- Application Information
AI Technical Summary
Problems solved by technology
Method used
Image
Examples
Embodiment Construction
[0017] The present invention will be further described in detail below in conjunction with specific embodiments.
[0018] According to attached Figure 1-2 shown;
[0019] The composite material / metal laminated structure composite pipe co-curing manufacturing method is characterized in that it includes the following steps;
[0020] 1) According to the size of the metal inner wall and the laying design of the blank, prepare a steel pipe with a certain diameter and a certain wall thickness as the blank laying mold, stick a layer of single-sided glued PTFE glass cloth on the surface of the tooling, and lay up two layers in sequence PTFE cloth, a layer of porous isolation film, a layer of AIRPAD rubber and a layer of non-porous isolation film;
[0021] 2) According to the layup design, lay up prepregs on the surface of the tooling in turn, and vacuum compact every 3~5 layers for no less than 30 minutes. After the prepregs are laid up, lay 2 layers of adhesive film on the surface...
PUM
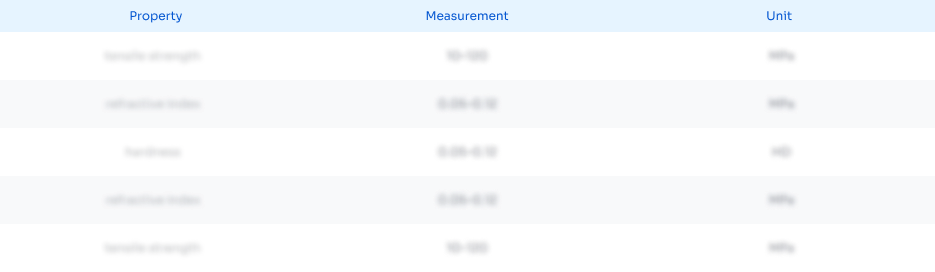
Abstract
Description
Claims
Application Information

- R&D
- Intellectual Property
- Life Sciences
- Materials
- Tech Scout
- Unparalleled Data Quality
- Higher Quality Content
- 60% Fewer Hallucinations
Browse by: Latest US Patents, China's latest patents, Technical Efficacy Thesaurus, Application Domain, Technology Topic, Popular Technical Reports.
© 2025 PatSnap. All rights reserved.Legal|Privacy policy|Modern Slavery Act Transparency Statement|Sitemap|About US| Contact US: help@patsnap.com